Key ways EMI Uganda’s experience in construction informs design
Construction Management in Uganda
Once a set of EMI drawings is released to a ministry partner, EMI may have little to no control over what gets built or how it gets built. The construction management (CM) program at EMI Uganda began in 2007 with a vision to build what EMI designed—to ensure that the construction followed the design intent. These construction services have become an additional way EMI can serve Christian ministries in Uganda. But the CM program has also grown to be an important ministry to the construction workers themselves.

EMI’s involvement in projects where the ministry hired a general contractor has often shown how little value is placed on construction workers. They are rarely paid on time, there is little to no training provided, and no investment is made in these workers—they are seen as a resource to be used. On projects where EMI Uganda manages construction, the workers are paid on time and they are regularly trained in different professional skills. This improves the quality of the work and allows them to find better employment after the EMI project is finished. A weekly chapel is also held to share the love of Christ with the workers and demonstrate their value as people created in God’s image. CM has benefited our ministry partners with well-managed construction, and has expanded the reach of EMI to disciple those working on project sites. But how is this construction experience informing EMI design?
Who will build this?
Seeing how EMI drawings have been interpreted and built over the past 10 years has allowed EMI to become better at designing appropriately. An important question to consider in the design process is, “What involvement will EMI have during the construction phase?” If EMI will have no involvement in the construction, there is no way to ensure that details will be followed. This means design should be limited to the concept level. Involvement in construction has also highlighted the importance of helping ministry partners consider the question, “Who is going to build this?” in the early stages of design. The answer to this question typically falls into three categories:
- Local Contractor: Small to medium companies familiar with building small projects with local construction techniques, methods, and materials.
- Commercial Contractor: Medium to large companies who are familiar with building larger commercial projects and meeting specifications and standards.
- EMI self-perform: Construction is done by a team of workers managed by EMI staff.
How does the selection of project contractor inform the design?
Selection of the project contractor informs the level of design detail. In Uganda, contractors often build from concept-level drawings, sometimes only a floor plan and elevations. Therefore, including too much detail may not be understood and will likely be ignored. The culture dictates that a contractor should know how to build as it is their occupation. It would be shameful for a contractor to ask questions about the drawings because they would be declaring either that they don’t know how to do their job, or that the designer hasn’t done their job properly. The contractor is used to filling in the gaps, so if they don’t understand or recognize the drawings, they will revert to what they are used to doing. Consideration must be given to what information and level of detail to include on drawings.
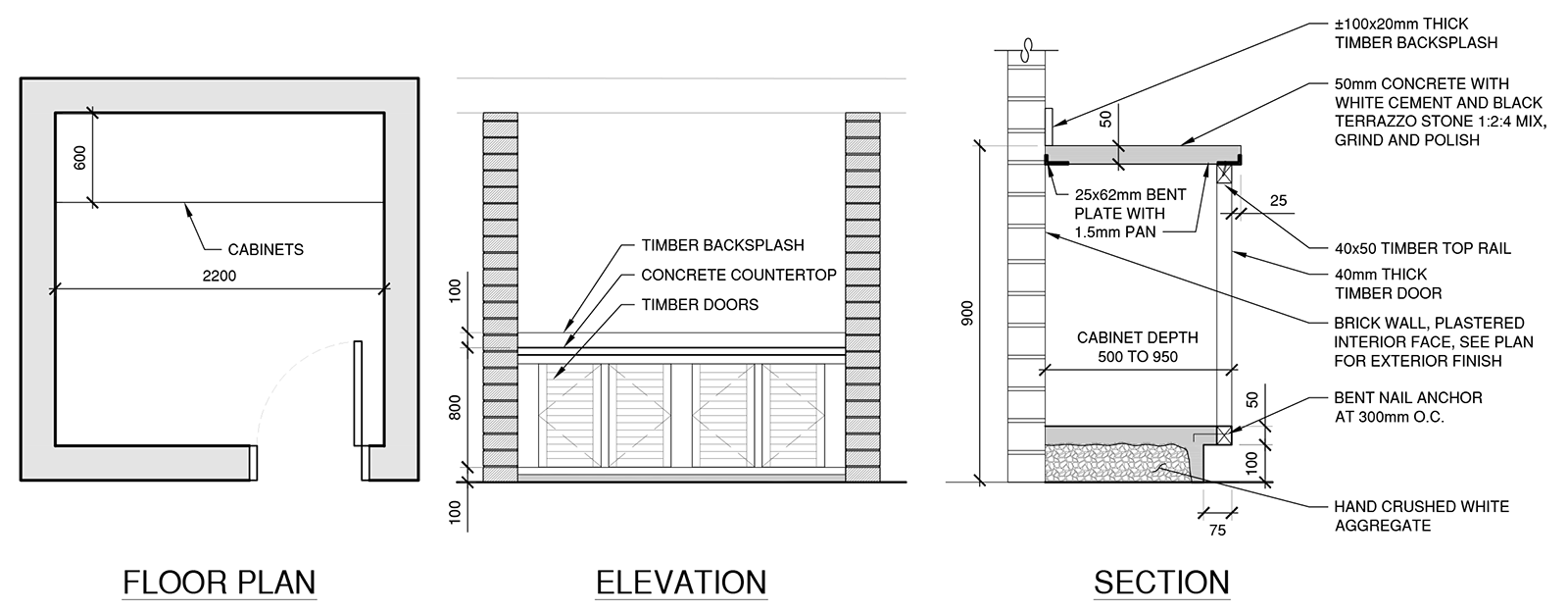
For local contractors, EMI should provide minimal detail and assume that the construction will follow existing practice. Improvements to safety can be made by selecting some critical details and making modifications to the existing practice. EMI can provide more information for commercial contractors as they would be more familiar interpreting drawings. However, even here the time spent thinking through and drawing details may well be a wasted effort. EMI Uganda has developed typical details for use in self-performed projects which differ from local practice either to increase tolerances to make installation simpler, or to save cost. When these details have been included in drawing sets sent out for bid, they have been quoted at a higher cost because the details were unfamiliar to the contractors. In general, the approach to drawings should be to simply communicate design intent so that the contractor can choose a detail they are familiar with. For EMI self-performed projects, drawings can be more detailed and developed in conjunction with the CM team to include the information required for them to build.
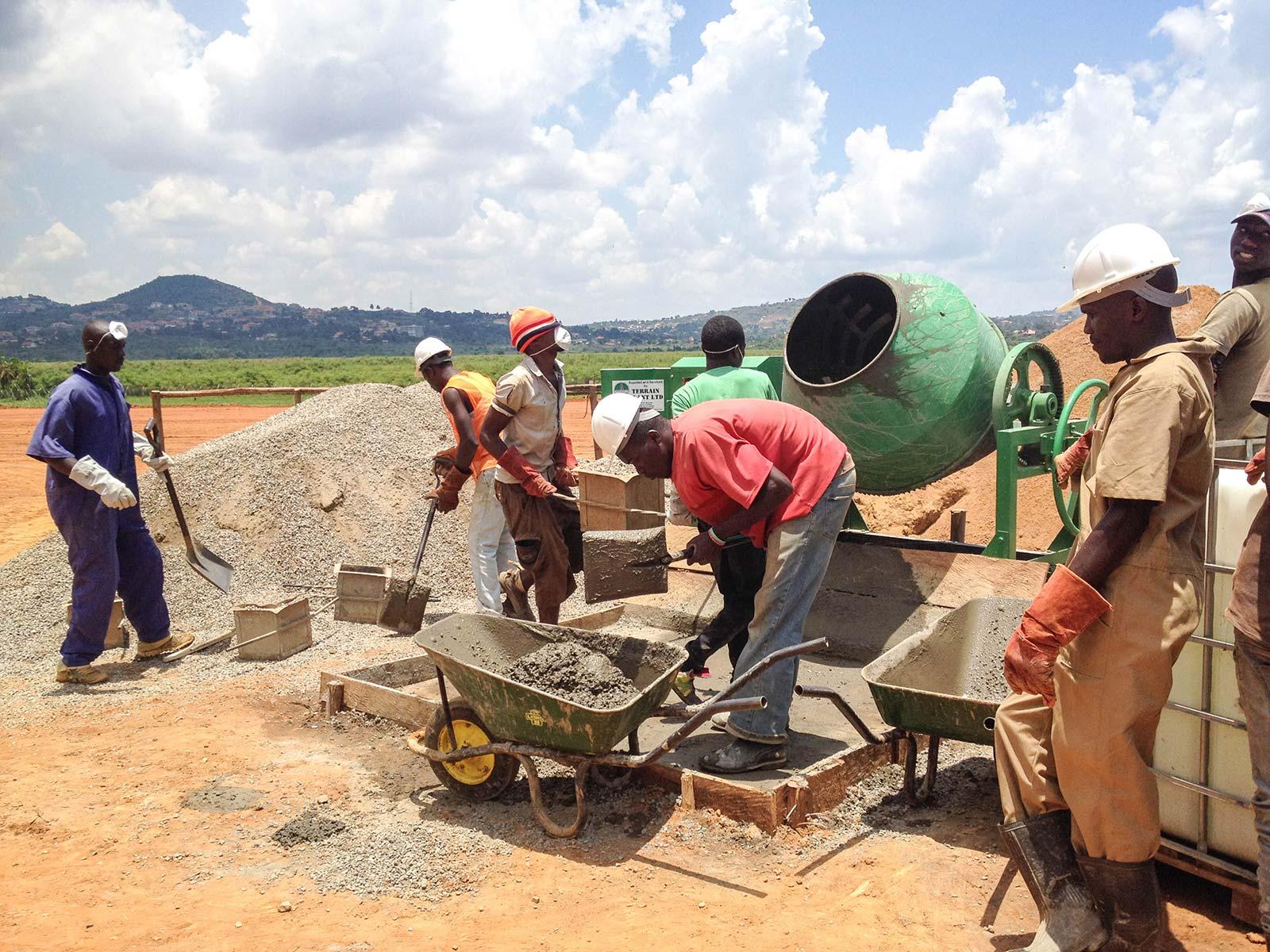
Construction experience also informs how concrete members are designed. In the developing world, concrete strengths can be low due to poor material quality and little or no quality control during the mixing process. Concrete is made from four main components: cement, fine aggregate (sand), course aggregate (gravel), and water. Through EMI Uganda’s experience testing concrete mix designs, the most variable of these components in Uganda is the quality of sand. The presence of silt, clay, and organic materials in sand (for instance in sand from lakes and rivers) reduces the strength of concrete. Contractors have varying levels of quality control in mixing concrete. Local contractors will most likely use lake sand and not do any concrete testing nor have much consistency from one batch to another. Commercial contractors will have access to better quality sand and will have experience with mix designs and concrete testing, thus allowing for higher design strengths to be considered. EMI Uganda has done mix design testing and can source better quality sand. It is common for EMI to adjust the design concrete strength and specify the concrete requirements depending on the contractor’s capabilities (see Table 1).
Type of Contractor |
Design Strength |
Concrete Specification |
---|---|---|
Local Contractor |
15 MPa (2200 psi) |
Cement to sand to aggregate ratio. Water to cement ratio. |
Commercial Contractor |
20-30 MPa (2900-4300 psi) |
Desired concrete compressive strength. |
EMI self-perform |
15-20 MPa (2200-2900 psi) |
Cement to sand to aggregate ratio. Water to cement ratio. Desired concrete compressive strength. |
Another important way that construction experience has informed the way EMI designs is in trying to retain local construction methods as much as possible. For example, there are different sizes of rebar available on the local market in Uganda: 6mm, 8mm, 10mm, 12mm, 16mm, 20mm, and 25mm. But local practice relies heavily on the use of 12mm bars. So while concrete elements may be more efficient and easier to construct by using a fewer number of larger bars, a design is more likely to get implemented if more 12mm bars are used. EMI regularly aims to improve the design standards of a given project, which likely means that more reinforcing steel is required compared to the local standard. However, by using bar sizes common to local practice, an improved design is more likely to be accepted and implemented.
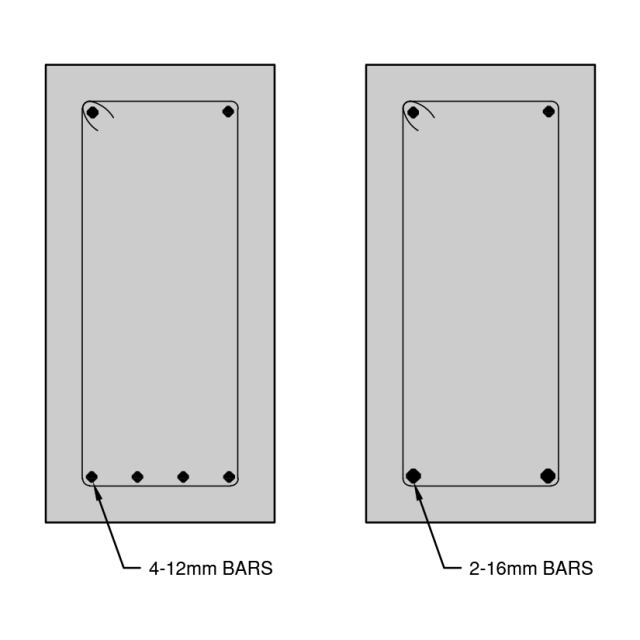
How can Uganda construction experience inform the broader EMI context?
EMI’s exposure to construction in the local context has influenced Uganda design work to be more appropriate. It is easy to see how this applies where EMI has field offices, but what about places without an EMI field office? Time should be spent at the start of an EMI project trip to explore the local area and investigate the construction practice. It is also essential to have diversity in our design teams. Critical input from local design professionals on an EMI design team will lead to more constructible and appropriate designs. Asking the question of the ministry, “Who is going to build this?” will lead to a better assessment of the level of detail the design work should contain. There is a time commitment to understanding the local construction practice and capability. However, this understanding informs design so that it is appropriate, glorifying to God, and a true service to our ministry partners.
The EMI Fund
The EMI Fund supports all that we do at EMI. With a strong foundation, we can keep designing a world of hope.
EMI Tech is looking for contributors – write to editor@emiworld.org with your topic and article outline.