Engineering Ministries International teams are usually very reluctant to recommend a wastewater treatment system that has any level of mechanization or sophistication. Staff and volunteers have seen how little priority is typically placed on wastewater system installation and maintenance, and thus know the short life expectancy of these systems in many developing world communities. Wastewater engineers know the critical need for any system to be designed with the maintenance personnel in mind. In the developing world, this many times implies limited technical understanding and ability to repair a given system. But engineers also know how important wastewater systems are to a community's health and environment, and want the best solution that can be reasonably budgeted for and maintained. While it is certainly not always better to have a more advanced system, in some situations a more sophisticated system may be worth considering. In the following case study of a wastewater treatment plant at a university in Nigeria, we will examine what aspects led to that system’s success and sustainability.
The Engineer's Tour
Benson Idahosa University started building its campus over ten years ago on the outskirts of Benin City, Nigeria. In the subsequent years, the city grew up around them to constrain the 7 hectare (17 acre) campus and its 2000 resident students. This incredible density has put a strain on all the infrastructure, especially the wastewater treatment and disposal system. Within four years of constructing the first buildings, the university had replaced the original simple septic tank systems with two aeration wastewater treatment plants. When EMI toured these plants six years after construction, both systems were still operating, and being well taken care of. They provide a vital upgrade from the previous over-capacity septic tank systems, while also paving the way for the projected expansion of the University to nearly 7000 student residents by 2022.
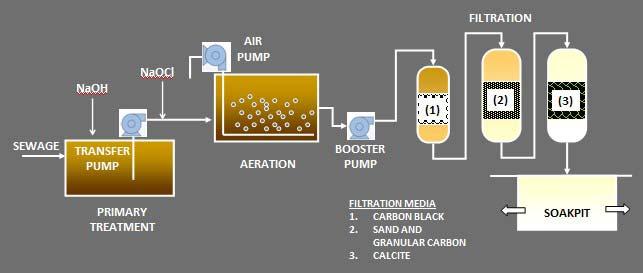
The treatment process currently in place for the over 150,000 Lpd (39,600 Gpd) of sewage generated at the campus is fairly sophisticated. It involves pretreatment, aeration, and filtration through “carbon black,” granular carbon & sand, and finally calcite media. Caustic soda is added at the primary treatment tank to create a pump-able slurry. Sodium hypochlorite is added for odor control. The treatment effluent is discharged into the ground through soak pits, although it was originally disinfected and discharged to a drainage swale on the site. The sand filters are backwashed every two weeks and the media is replaced every three months. The primary treatment and aeration tanks are de-sludged every six months to one year. Notably, the treatment process for the two systems is batched on a daily basis rather than operating on a continual flow basis.
A Good Fit
The university had a lot going for it to make this complex solution a good fit. The original design engineer from Norway invested a good deal of time in the project. He had spent a significant amount of time on site to determine the best process given all the operational constraints for the University. Then, after the design stage, he spent time to oversee construction, test and tweak the process, find a reliable source of chemicals, train the local engineer and the University maintenance personnel, and impart the importance of following a rigid protocol for handling the chemicals. Years later, the evidence of his investment was apparent during our visit.
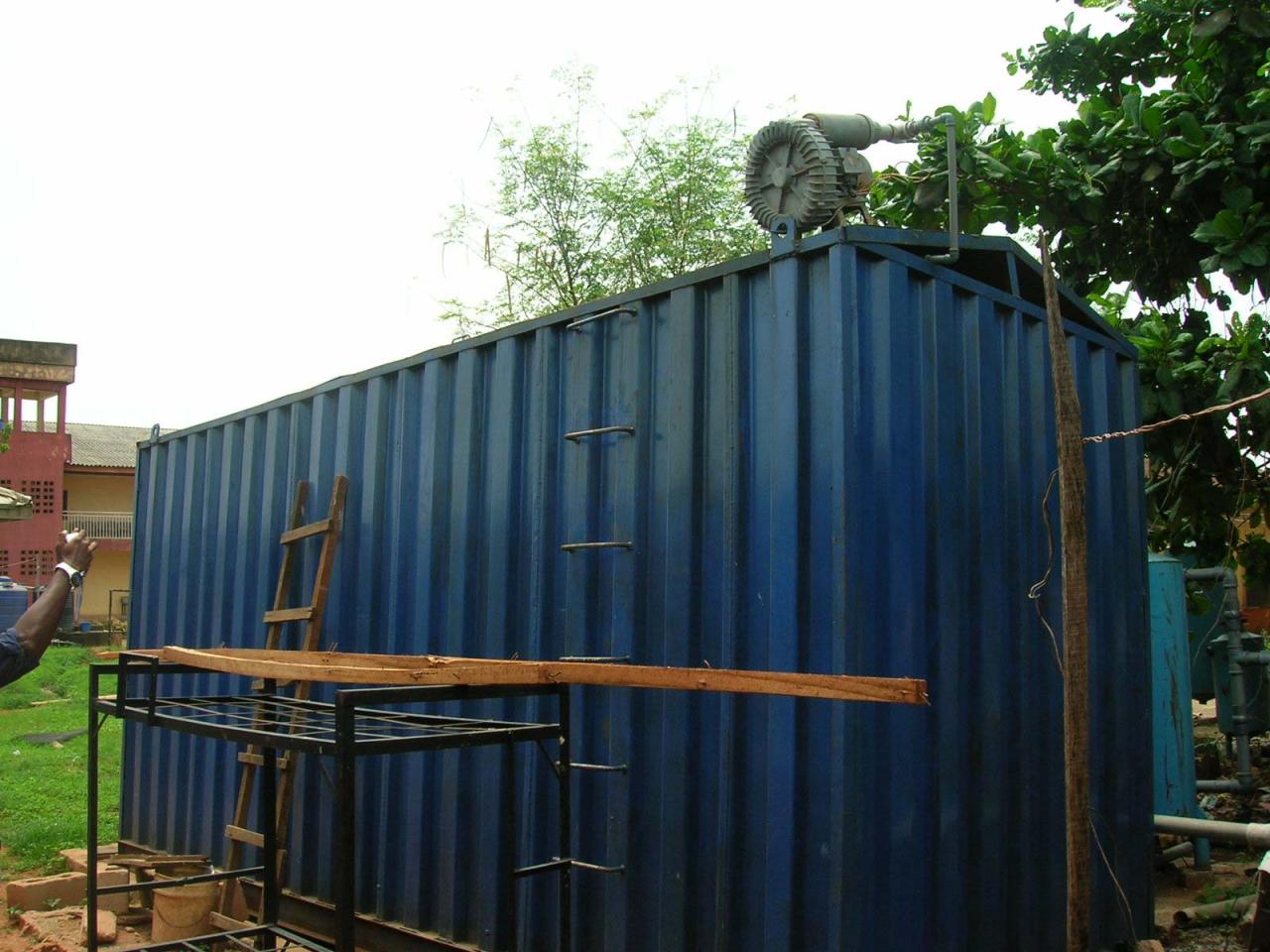
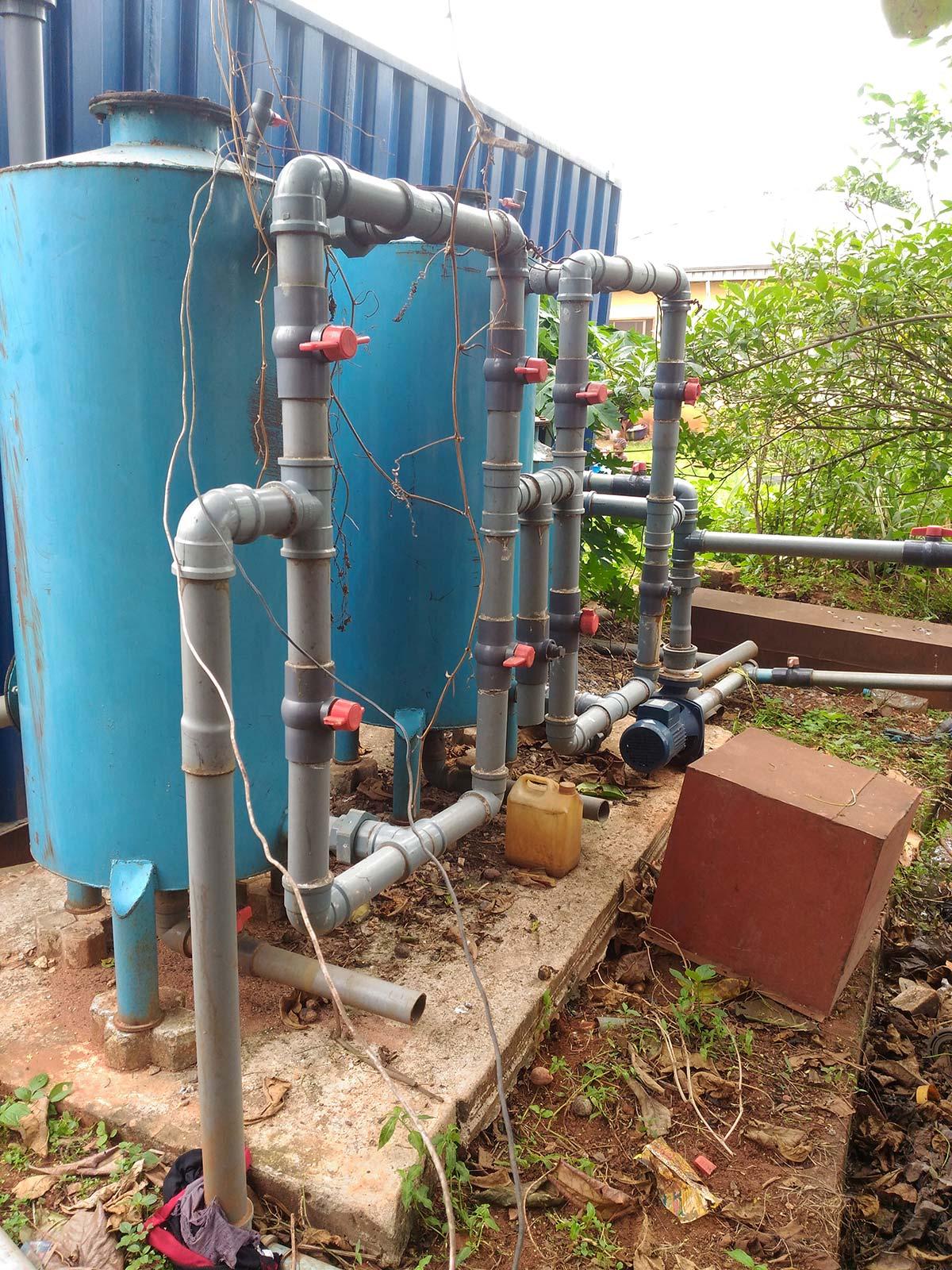
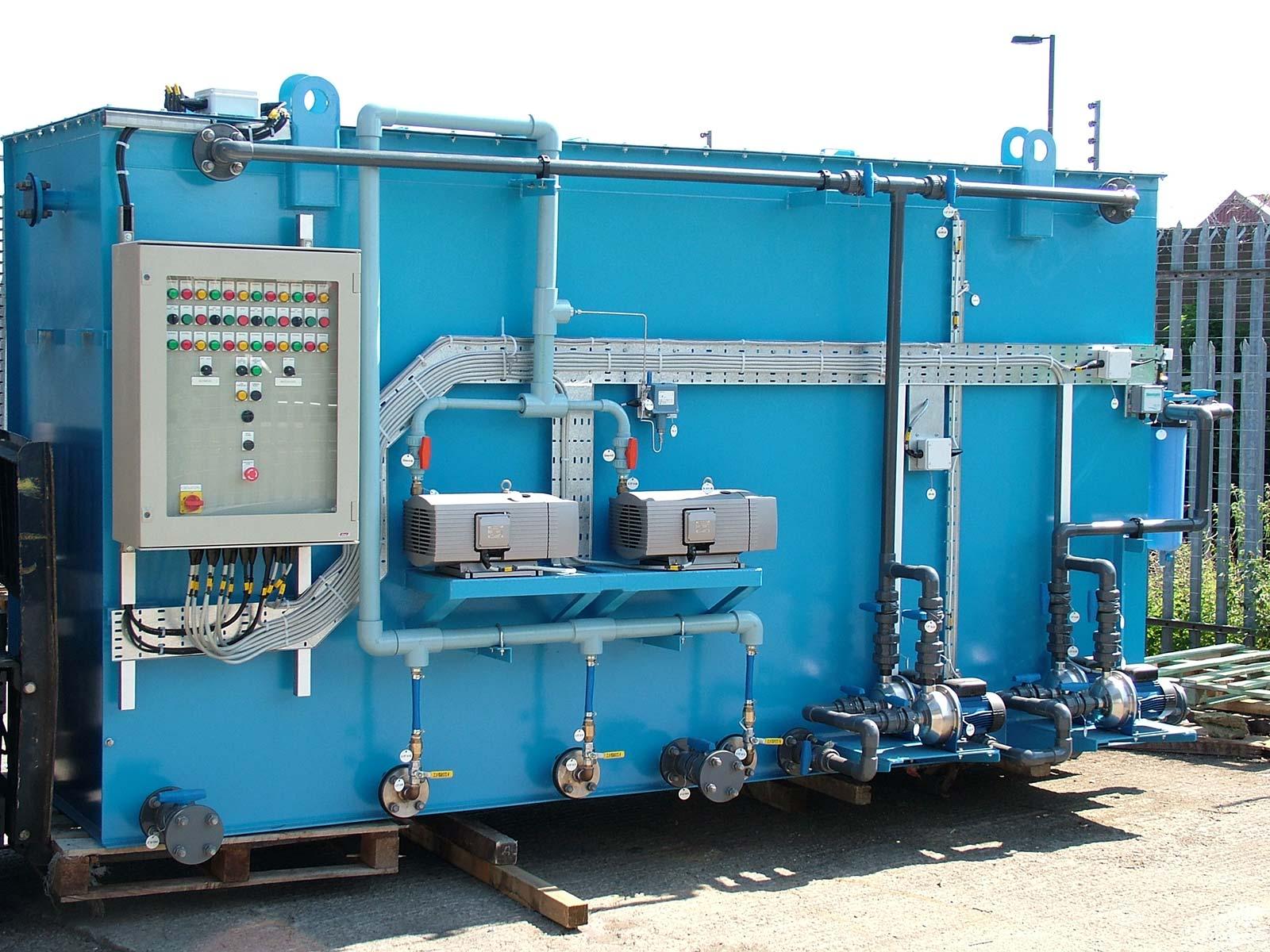
The treatment process being implemented was not new, and could not be considered a complicated system. These biological and chemical processes are being used around the world in much larger applications. It would have been very easy for the design engineer to specify a package treatment plant from a foreign supplier. But instead of using an off-the-shelf product, the designer chose to take the time to custom-build the plant with materials and equipment he could find locally. One of the ways the treatment process technology was kept simple was to make sure the treatment processing was done in daily batches. Many similar systems will treat effluent on a continual-flow basis which requires much more vigilance of the system. This often will necessitate monitoring equipment, metering pumps, floats and alarms. However, in this case, the design specified that the influent tanks would fill during the day time, and then maintenance personnel would operate the treatment system every night by following a rigid protocol. As a result, the design of the treatment system did not require complex equipment which may be more susceptible to break down. The outcome was a process which was both fully manual and fully repairable by local technicians – with no proprietary equipment or chemicals. This system's operation is complex enough to require a local engineer who is on staff at the University. He fully understands the treatment process and periodically tests the effluent, tweaking the process as necessary. However, the University already had technical people on staff and so either training existing staff engineers or bringing in another engineer was very realistic in this situation. In any case, it was an advantage that the University had technical people ready to jump in when the design engineer left town. Another reason this system has performed well is that it is located in a larger city where supplies and parts can be readily purchased or ordered in, and where tradesmen can be found on short notice to make repairs as necessary. Finally, one of the drivers for moving toward this more sophisticated system was the huge ongoing costs of de-sludging the original septic tanks. Prior to the installation of the treatment plants, the University was spending USD 4500 monthly to haul raw sludge to the municipal landfill. And this cost would only rise as the University expanded its student resident capacity. Once the administration realized how great the present and future cost savings would be with the new treatment system, they were ready to move ahead with the project. Now the University’s operating costs for salaries, chemicals, and the greatly reduced sludge-hauling have now been cut down to less than half.
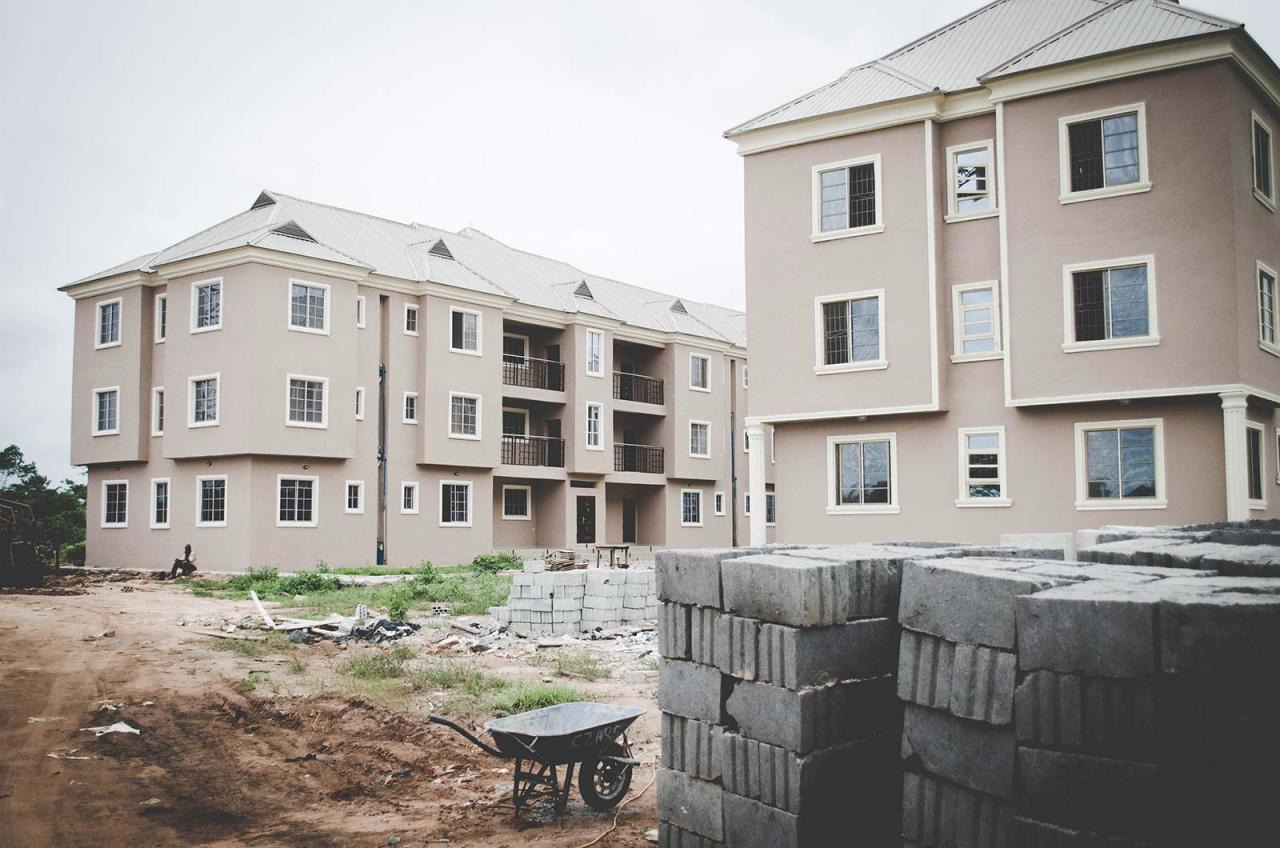
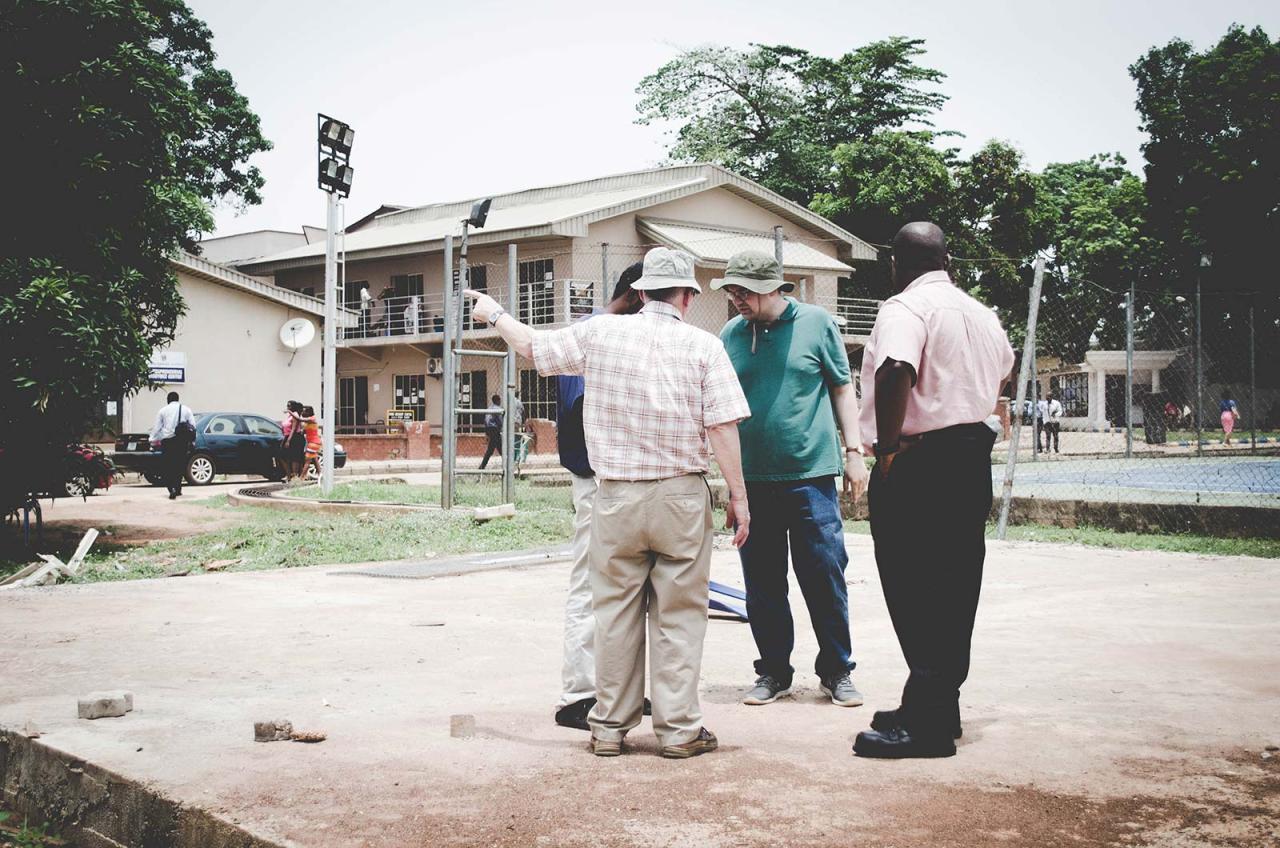
Our Role
On many EMI projects, we tend to focus on simple solutions such as septic tanks and soak pits because they are simple and mostly maintenance free. For the non-tech-savvy environments most of these projects are located in, these are often the best solutions. But there are projects where more complex systems are not only more desirable, but may be required. This could be due to higher operating costs of simple systems, or due to the project’s location in a dense, urban environment. Whatever the cause, the local context must be clearly ready for a more complex solution. To follow on the success of the example from Nigeria, design engineers will need to spend significant amounts of time refining the wastewater system design to make it locally appropriate and locally repairable. The location of the project must be such that the needed resources – chemicals, parts, and technical people – are all readily available. The design engineers need to be available during and after construction to train and empower local engineers / technicians to maintain the system and make alterations to it over its lifetime. In these situations, our experience has been that wastewater treatment system equipment specified off the shelf is likely to fail in the long-term. But if we ensure the technology is appropriate for the local context, and that the local context really demands a more complex solution, the success of the Benson Idahosa system can be repeated.
The EMI Fund
The EMI Fund supports all that we do at EMI. With a strong foundation, we can keep designing a world of hope.
EMI Tech is looking for contributors – write to editor@emiworld.org with your topic and article outline.