Learning from the forensic diagnosis of distressed CEB buildings in West Africa
We headed to the project site in West Africa with the thought that the compressed earth block (CEB) buildings which composed most of the campus were experiencing distress due to poor construction practices. This notion was partially created from a brief preliminary investigation by EMI, and partially created from descriptions of the distress by the ministry. However, upon further evaluation of the CEB distress, it became apparent that the CEB was generally well constructed. We determined that a combination of other factors such as building design, site conditions, material defects, etc. had caused the distress.
Benefits
It is fairly easy to understand why the client would choose CEB as the main construction material to build the multiple single-storey buildings on their campus. CEB has become a popular form of construction in much of the majority world. It has also gained popularity in the United States, mainly due to the recent focus on sustainability and “green” construction. Benefits of CEB construction include sustainability, insulating properties, local availability, low cost, and aesthetics.
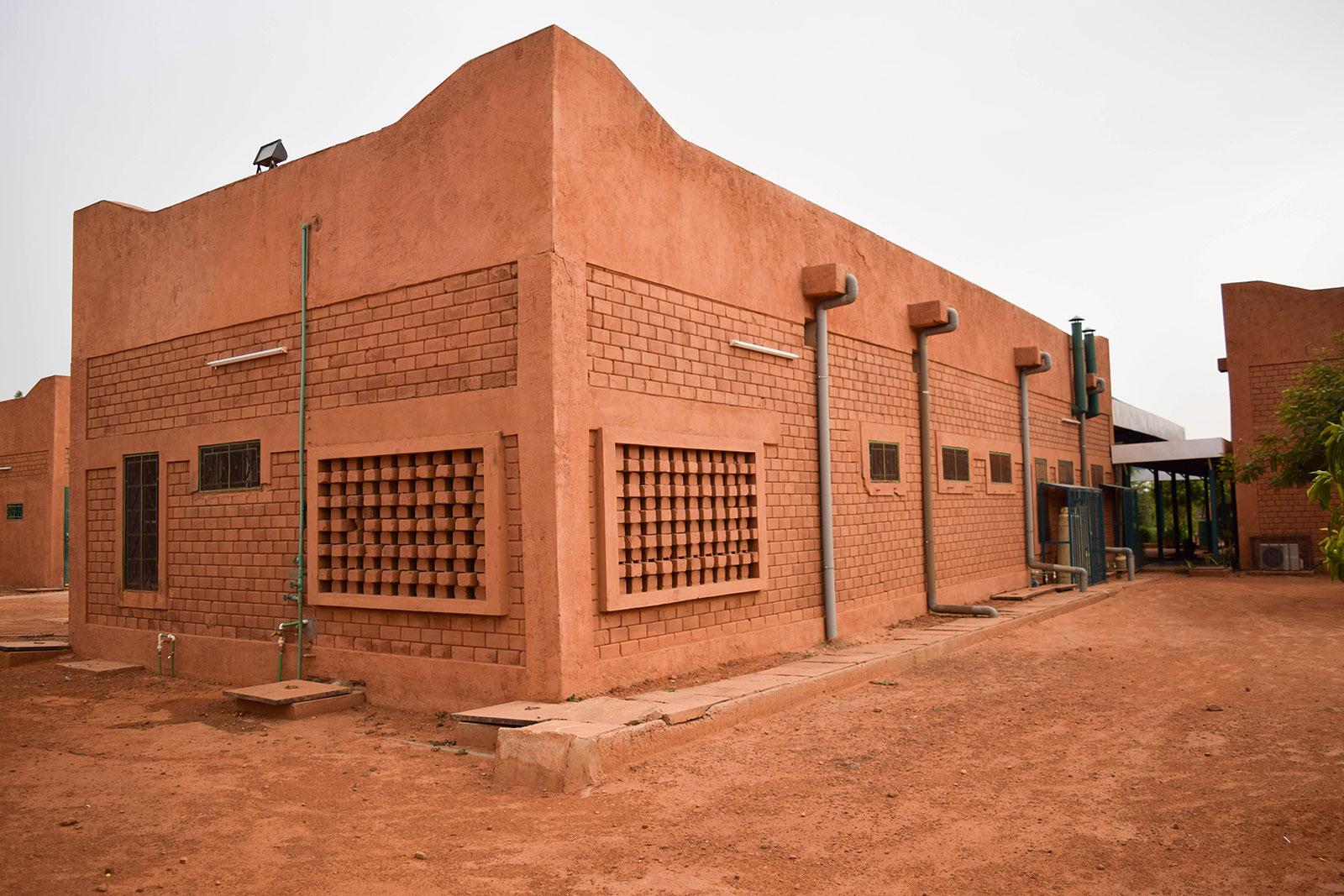
CEB is a sustainable form of construction because it is mostly composed of soil – a natural resource in great abundance. Due to their significant thermal mass, CEB also provides better insulation than other common building materials (e.g., concrete blocks). In hot climates in particular, the natural insulation from CEB allows for more efficient air conditioning of interior spaces or keeps non-air-conditioned spaces cooler for longer periods of time. Also, the soil for CEB can generally be sourced from local soil. Sourcing the soil locally instead of importing or shipping other wall construction material reduces overall construction costs and can benefit the local economy. CEB is also a lower-cost construction material than conventional concrete block due to its low cement content. Decreased cement content also leads to decreased environmental impact from CEB production. In addition to the economic and environmental benefits, CEB has a distinct appeal to many architects due to its modular construction and natural aesthetic. Part of the aesthetic of CEB comes from the ability to ‘dry-stack’ or construct CEB walls without mortar in block joints. However, dry-stacked construction is generally limited to non-load-bearing walls. It is likely that many or all of these factors played into the decision to use CEB to construct the buildings on the campus.
Common Problems
While CEB has many benefits, improper application of general structural design principals and CEB-specific design recommendations, combined with a lack of consideration of material characteristics can lead to both cosmetic and structural distress. Information relating to these aspects, as well as best construction practices, is available in documents such as “Compressed Earth Blocks: Manual of Production,” by Vincent Rigassi. Despite this, engineers and laborers in the majority world often revert to traditional design and construction practices learned through years of experience. It is possible that this contributed to the distress observed on the campus.
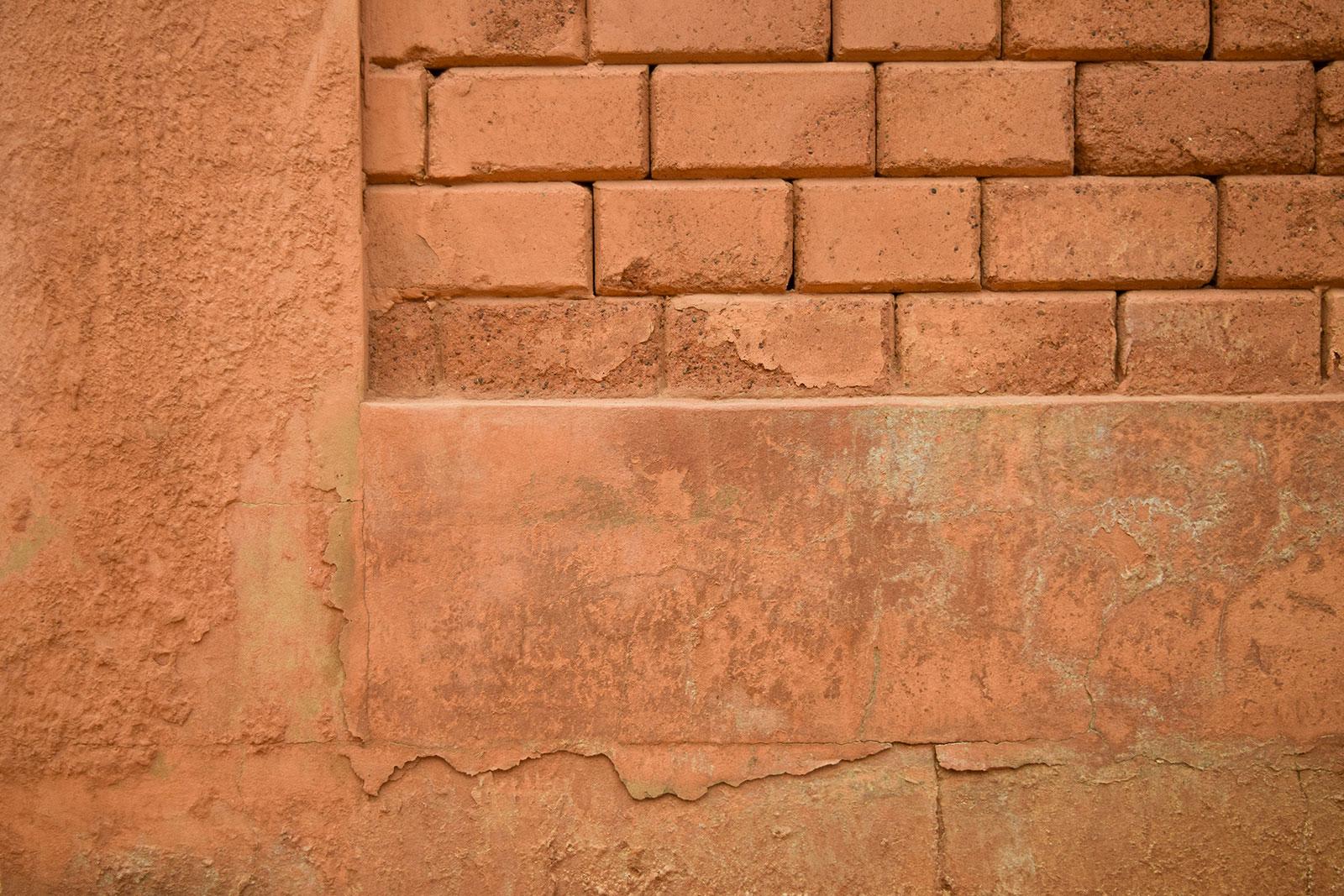
Deterioration
The most prolific form of distress observed in the CEB buildings was deterioration of the exterior (and sometimes interior) face of the blocks. While CEB is a breathable material with a natural ability to absorb and release moisture from the air and regulate humidity, it is susceptible to deterioration when exposed to direct moisture (e.g., runoff from leaking gutters or driving rain). For this reason, best construction practices indicate that exposed CEB should be stabilized in order to improve its ability to withstand weathering. CEB stabilization is generally achieved by adding cement or other constituents into the mix design. Other examples of stabilizing materials include fibers (synthetic or organic), clays, or bentonite. Although purchase orders at the time of construction indicate that stabilized CEB were specified, the widespread deterioration was a clear indicator that stabilization was not properly implemented during the block production. This deterioration has also been aggravated by a host of moisture sources in addition to general humidity and rain. These sources included A/C drips, A/C units, broken drain pipes and gutters, leaking storm water and sewer lines, and daily cleaning operations. The deterioration we observed was only cosmetic in nature. However, if proactive measures are not taken to mitigate continued deterioration, there is potential for structural concerns to develop.
Concentrated Loads
Two buildings on the campus were constructed with concrete roofs. Due to the significant weight of these roofs and the span requirements in some of the rooms, both roofs were framed with concrete beams. Several of these beams framed directly into interior corners of CEB walls and therefore induce a large concentrated load at the top corner of the wall. Although these walls are load-bearing, many of the typical details recommended in load bearing walls were either left out of the design or not implemented properly during construction. If CEB is used in a load-bearing wall application, there needs to be a way for individual blocks to support the design loads and transfer them to the foundation below. Details such as mortaring block courses, constructing continuous bond beams (i.e. lintels) above door and window openings, and placing vertical and/or horizontal reinforcement in the walls are all ways load-bearing walls can support and transfer concentrated loads adequately.

Unfortunately, none of these techniques were effectively implemented at the campus. Our observations seem to indicate that the design called for these walls to be constructed as dry-stacked CEB without mortar or reinforcement. It was also evident from construction photos that many of the lintels were not continuous. The only detail included in the CEB wall design that promoted load transfer was the keyed geometry of the block, allowing for mechanical interlock between adjacent horizontal blocks. The lack of proper detailing for load-bearing CEB walls has resulted in through-thickness diagonal wall cracks. These cracks were evident in walls supporting beams near corners and in adjacent walls. Due to the severity of the distress at a few isolated locations, we recommended structural repairs. Because it was not feasible to install mortar or reinforcement in the existing walls, our repair detail consisted of removing a portion of the CEB wall beneath the beam causing distress and replacing it with a reinforced concrete column. The repair also required widening the concrete footing below the new column. A typical construction detail for this repair is below.
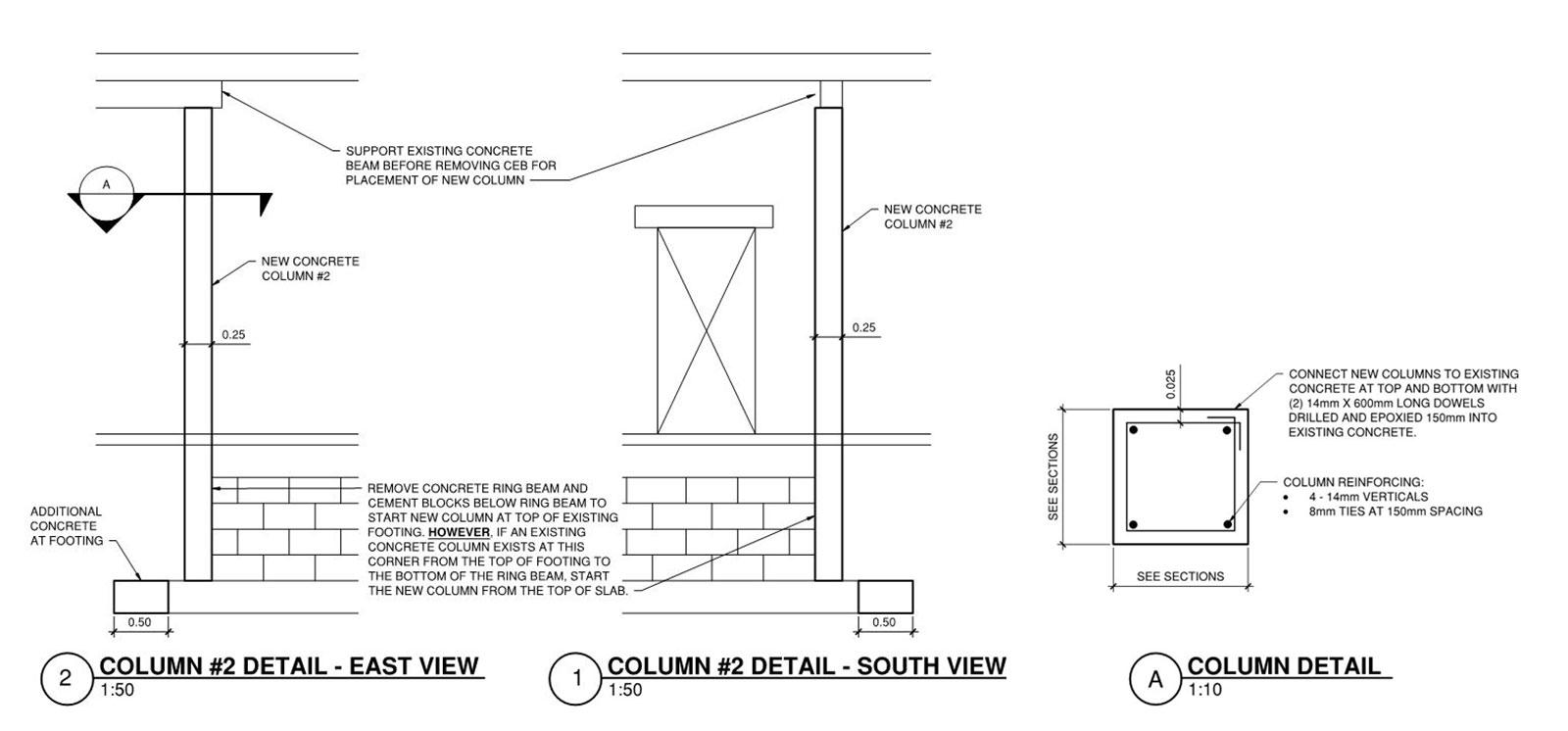
Settlement
Settlement is a widespread concern throughout the campus that has also caused distress to the CEB buildings. Due to the nature of settlement as well as the variety of factors contributing to it, the settlement across the campus and even across the footprint of individual buildings was not uniform. Observations indicated that concentrated loads at CEB wall corners may be overloading the foundations and causing them to settle. However, settlement is an over-arching issue on the campus due to poor soil composition, poor soil compaction, and excess moisture in the soil. CEB is similar to brick or masonry construction in that it can tolerate only minimal differential movement before cracking. Cracks in the CEB walls due to settlement manifested more as gaps between individual blocks than as cracks through the blocks. Most of the cracks due to settlement only indicated serviceability issues, not concerns of a structural nature.
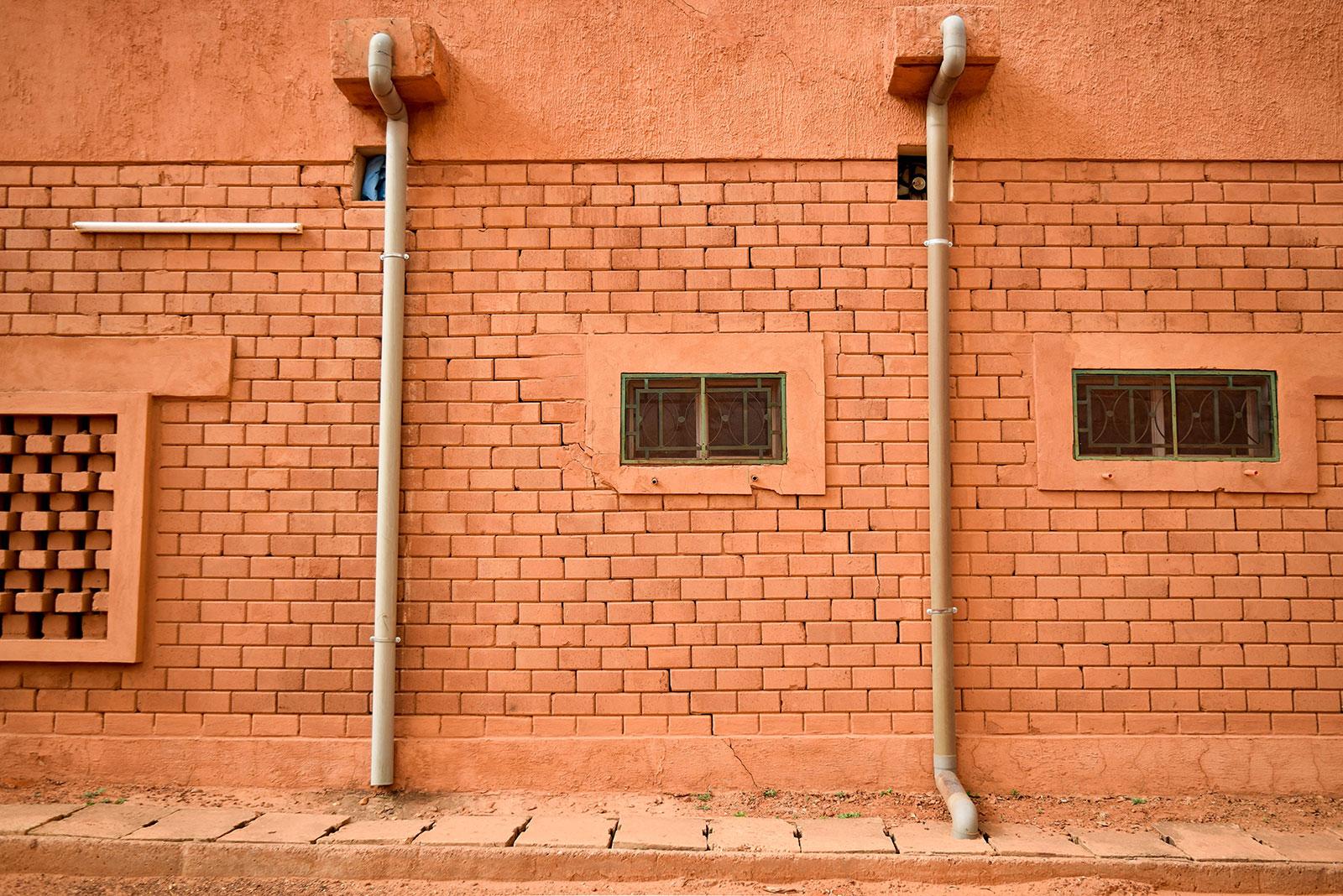
Summary
In recent years, compressed earth block has become a popular construction material due to its sustainability, low cost, local availability, and aesthetics. When CEB buildings are designed and constructed based on structural design principles and industry knowledge, they are a great option for simple, single-storey structures. However, if the design and construction of a CEB building does not account for the inherent weaknesses of CEB, distress of both cosmetic and structural nature can occur such as that observed on this campus. The main areas of oversight in the CEB buildings on the campus included: adequate stabilization of the CEB, design detail for load-bearing walls, and evaluation of differential settlement potential.
The EMI Fund
The EMI Fund supports all that we do at EMI. With a strong foundation, we can keep designing a world of hope.
EMI Tech is looking for contributors – write to editor@emiworld.org with your topic and article outline.