Exploring improvements to how EMI approaches geotechnical investigation and reporting
EMI project trip teams are often well-rounded with representatives from most major building and site design disciplines. However, one profession frequently overlooked is geotechnical engineering. Whether due to the often straightforward design of many EMI buildings or the specialist nature of the equipment, tools and data a geotechnical engineer requires to do their job, historically most EMI design teams forego geotechnical engineers. Typically, when an engineer needs to design a building foundation or retaining wall, a pit is dug down to the proposed foundation depth, the soil type is roughly determined using the “Texture by Feel” procedure, some rules of thumb are applied, and a safe round number is assumed for bearing capacity, unit weight, or angle of repose. This simple procedure has been the approach for EMI India since its founding in 1998. But in the last 2 years, they (along with many other EMI offices) have been exploring a few improvements to the process.
One simple enhancement is the addition of a hand auger as a standard piece of equipment on project trips. In the right soil conditions, a hole can be augured in as little as 10 minutes. The soil that is brought to the surface can then be examined to determine its basic properties. The inclusion of a hand auger is especially useful if the site is large with buildings spread out over many different areas. The ability to dig more holes and deeper holes also helps determine if the sub-surface profile varies significantly or not. Often extendable up to a length of 3m, a hand augur is also useful when trying to establish the depth of a relatively shallow harder strata for placing building foundations. These augured holes are also very useful for determining soil types to aid in wastewater planning, as the soil types in several holes can be correlated with data from a percolation test in a hand-dug hole. Alternatively, with the addition of a water level probe, teams can perform percolation tests in the augured holes.
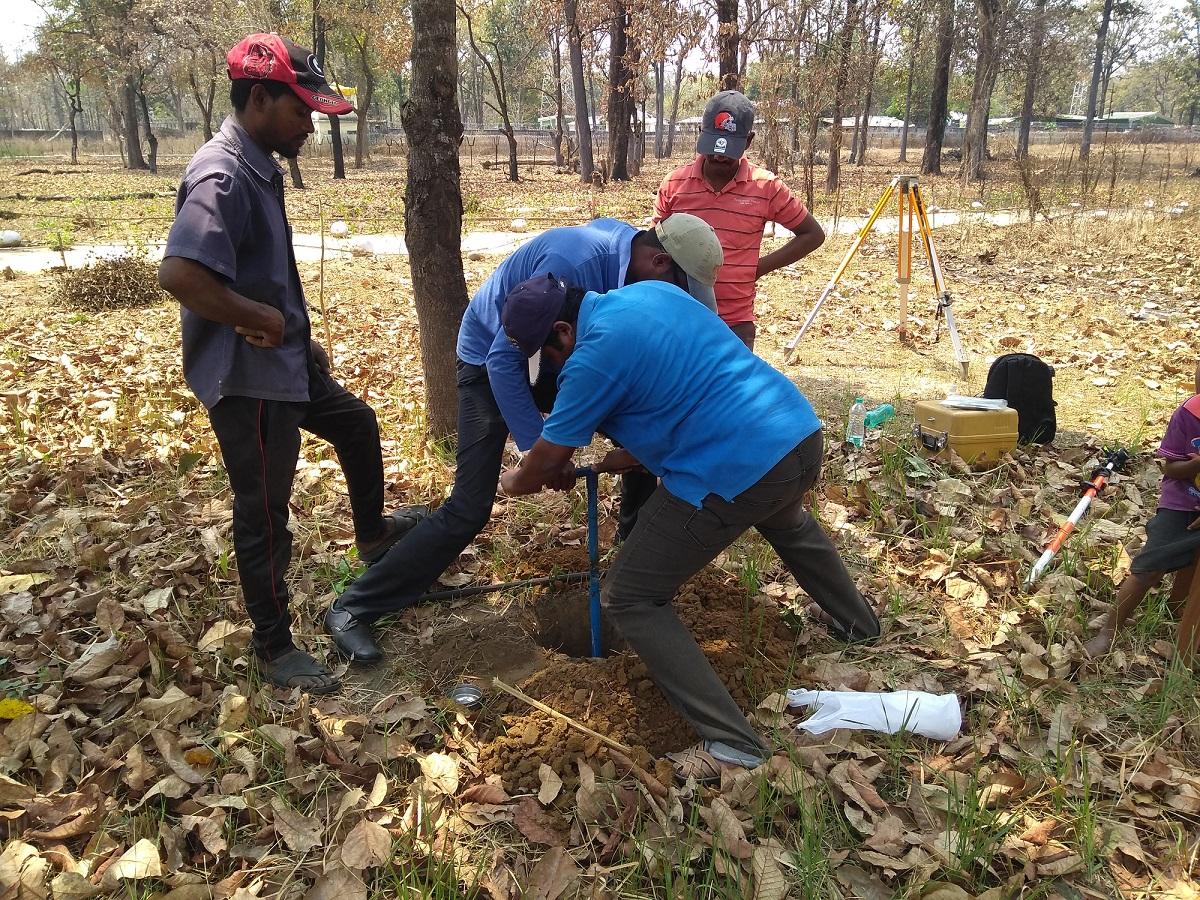
As referenced in a recent EMI Tech article, a portable sieve shaker is another way to improve the accuracy of the soil classification over the Texture by Feel method. The different sized sieves allow the engineer to visually estimate the percentage of soil at each gradation, which can then be applied to the USCS or similar soil classification charts. Although this method may not be as accurate as laboratory tests, in the hands of someone with soil mechanics experience, it can still be quite useful for many situations and represents a major improvement over standard EMI project trip methods.
A third improvement option is to bag up a few soil samples and deliver them to a testing lab for an exact soil grain size analysis by mass and Atterberg limits, both of which allow accurate soil classification. For projects that may involve significant earthwork, dry density and optimum moisture content can also be determined with these same samples. If the project is in or near a major city, it should be possible to find a soils laboratory. EMI India recently utilized this approach for a retaining wall design. The client sent a 10kg bag of soil to Delhi, and it was transferred to a local lab for classification. This created a more accurate estimate of the parameters required for the structural design of the retaining wall.
Despite the benefits these improvements may bring, some projects demand a more detailed exploration. While these may be non-typical for EMI, the India office encountered a number of such projects last calendar year. As EMI continues to evolve, there is potential to see more projects of this nature.
A more thorough investigation becomes necessary when a large amount of earthwork is expected or where slopes (whether existing or to-be-constructed) may have stability issues. Such was the case with a 750m runway in rural Myanmar for Mission Aviation Fellowship. The large scale earthwork design originally involved more than 250,000 m3 of cut and fill, up to 20 vertical meters of fill, sloped embankments, and an asphalt runway built to international aviation standards.
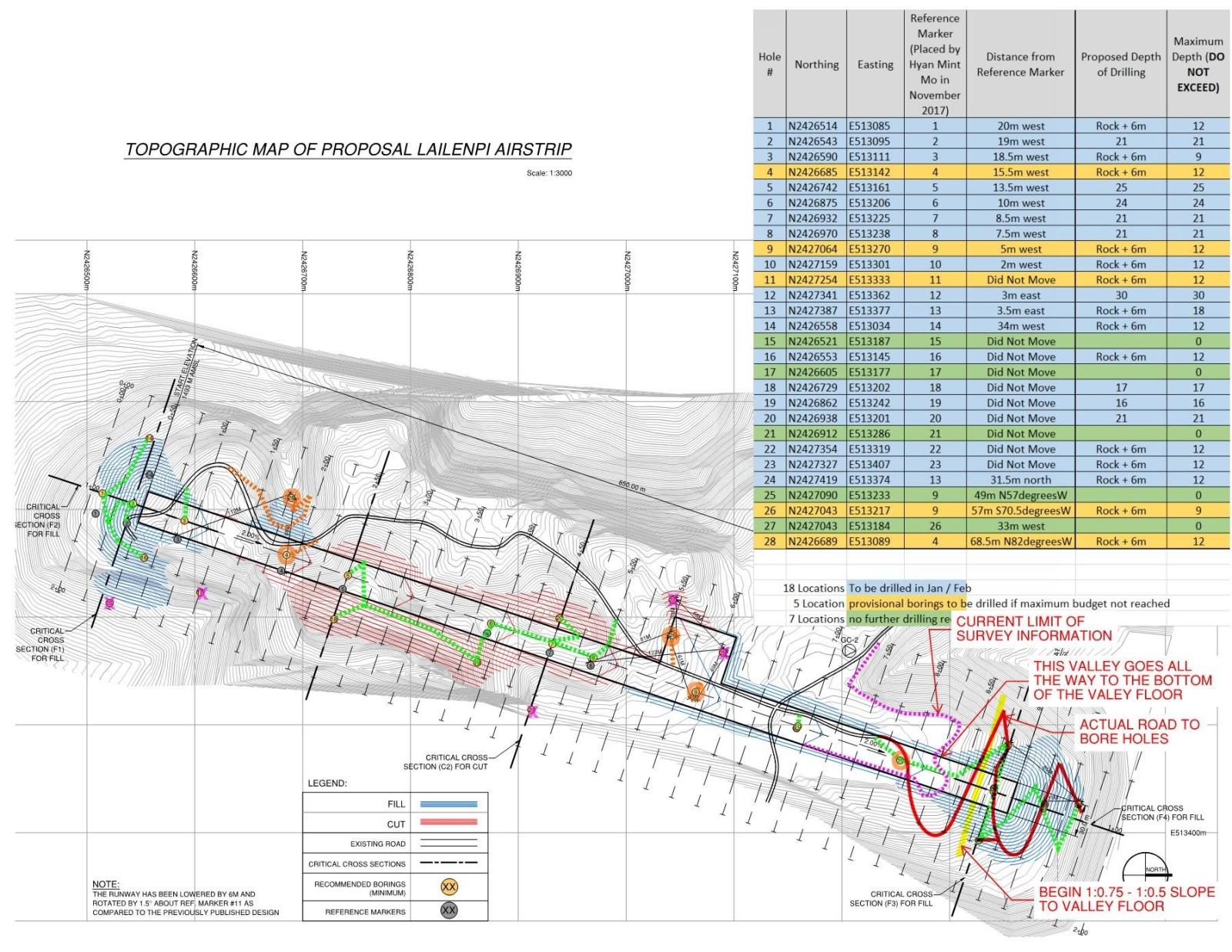
At EMI’s guidance, a geotechnical firm was hired and the program set to include 28 hand borings to a maximum depth of 3 to 5 meters and 20 deeper borings with a tripod mounted diesel drill to depths ranging from 7-30m. Once the boring was complete (which was intermittently overseen by an EMI staffer to ensure proper procedural adherence), the engineers expected the calculations, recommendations, and dialogue with the geotechnical firm to be similar to how the geotechnical industry works in North America. Eventually they realized that the geotech was acting more like a medical laboratory running blood tests; the results are provided, but the doctor must read those results and prescribe action. Thankfully, EMI Cambodia (and EMI’s only staff geotechnical engineer) was able to incorporate the geotechnical information into slope stability and other relevant calculations needed for the earthwork design. With this information, EMI designed the airstrip and is currently overseeing its construction.
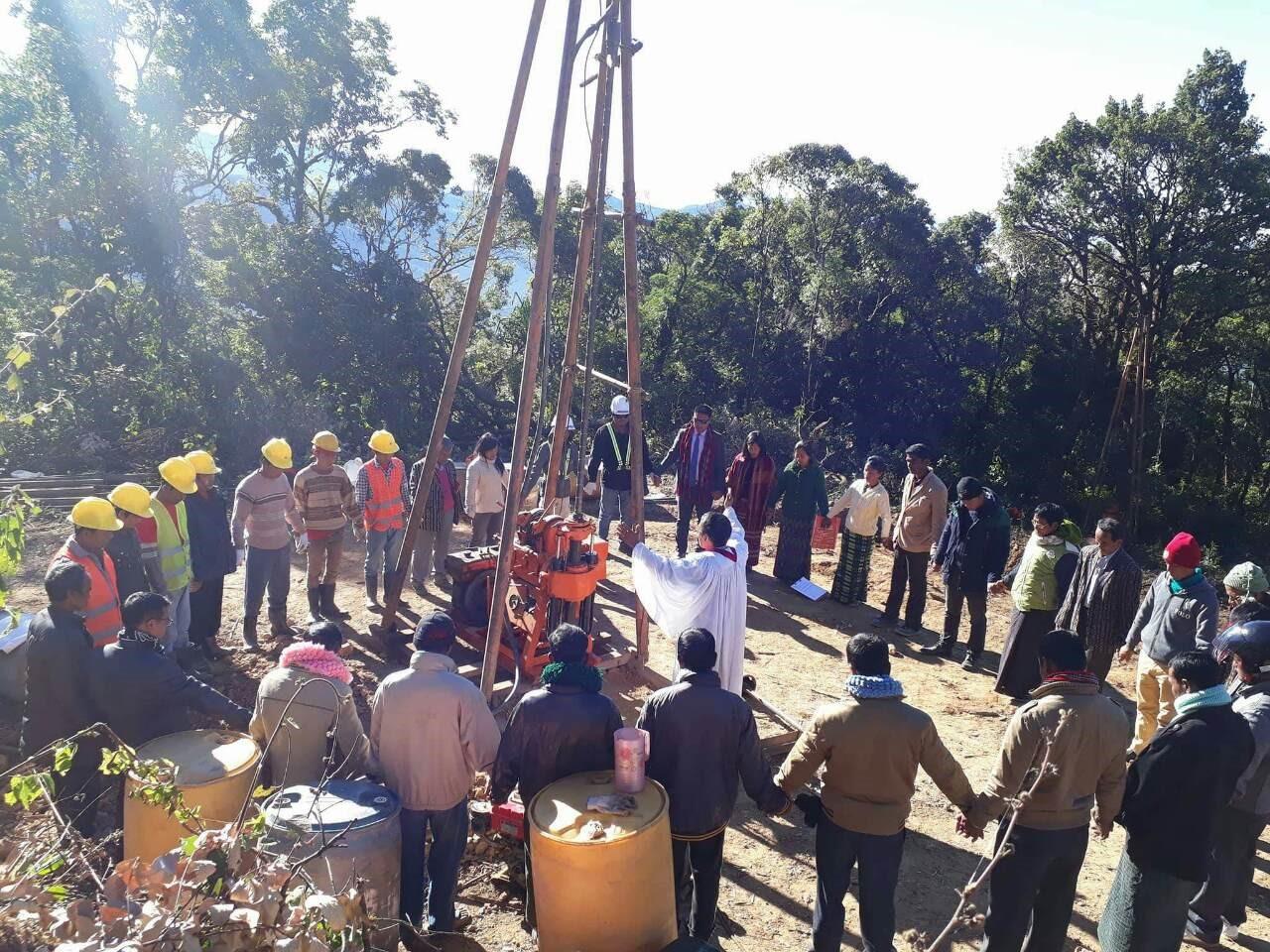
Another case when more geotechnical exploration becomes necessary is when a project requires complex foundations due to soft or swampy soils. Many locations within low lying portions of Southeast Asia require nearly every multistory building to be placed on some sort of improved foundation beyond simple spread footings. Such was the case in Kathmandu, Nepal, where EMI designed a 6-story dormitory to rest on a 2’-6” raft slab. Or in Cambodia, where placing buildings on driven pre-cast concrete piles is the norm. Anywhere piles are expected to be used or a raft/mat slab is the standard, EMI designers should require the client to obtain a geotechnical investigation to help with the more complex foundation design. Luckily, in the areas of the world that regularly require such foundations, there are usually at least a few competent geotechnical companies with the needed credentials.
Lastly, when a relatively light building will be placed on expansive soils, greater geotechnical investigation should be sought. On a recent project in India, the client had performed a geotechnical study on the site several years before EMI became involved. Upon reviewing the report, the engineers noticed a probable presence of expansive clay (locally called “black cotton soil”) in the top 10m. The original tests, although noting the clay content of the upper strata, did not investigate the expansive potential of the soil. A relatively lightweight steel framed building was planned for the site, and the water table is variable given the monsoon rain patterns. Consequently, EMI assisted the client in finding a geotechnical firm to perform additional borings and run the specific tests required to gauge the expansive qualities of the soil: the free swell index and swelling pressure in each layer.
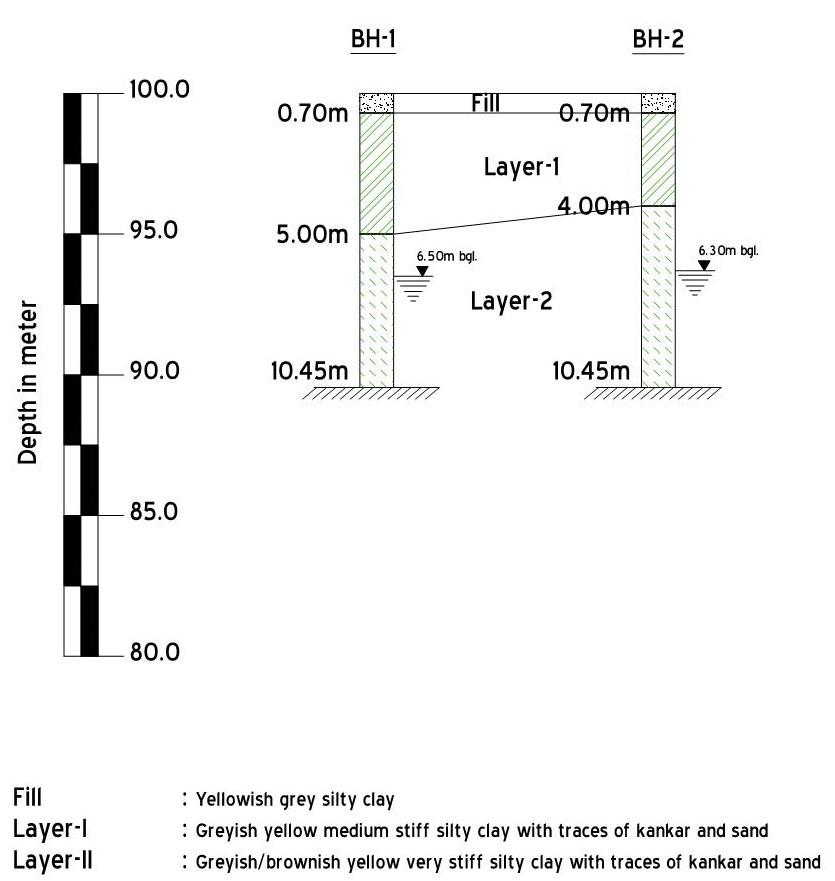
The geotechnical investigation confirmed that the clayey soil had moderate to high swell potential. Unfortunately, it was unclear if the weight of the structure and basic soil swell mitigation techniques would be adequate to negate the issue. If higher swell potential in the soil had been discovered, then it would have been obvious that drastic measures would be necessary: abandonment of the site for the designed purpose, huge excavations of clay, or under-reamed piles with sleeves. If the soil had less swell potential, then the building and overburden would provide enough dead weight to keep the soil from expanding. However, since neither of these was the case, the building’s foundation resides in a grey area: between a rock (actually a stiff layer) and an unpredictable expansive soil.
In an attempt to find a middle ground, EMI has recommended a structural slab with a one foot gap beneath the slab and soil, and an apron to keep the soils from fluctuating drastically in moisture content.
As EMI gets more involved in the construction and execution of design projects, greater geotechnical investigations are needed. EMI’s project teams need to do more in the field, and EMI design teams need to know when to call in local consultants for geotechnical study. This greater attention to what we’re building upon will create superior designs and better facilities that bring hope.
The EMI Fund
The EMI Fund supports all that we do at EMI. With a strong foundation, we can keep designing a world of hope.
EMI Tech is looking for contributors – write to editor@emiworld.org with your topic and article outline.