Evaluating wall materials available for projects in East Africa
As in many parts of the world where EMI works, the structure of a building in East Africa will most likely be some type of concrete or steel frame. The question is what to build the walls with? Typical infill materials available in East Africa are: Compressed Earth Blocks, Local Brick, Factory Brick, and Concrete Blocks (CMU). We will review each of these options below to summarize an ongoing investigation by EMI Uganda’s Research & Development department.Note 1
Compressed Earth Block
Compressed earth block (CEB) has several advantages. It can be one of the least expensive options since the bulk of the material is simply earth dug up on the site. The block mixture should include a small amount of cement and possibly sand, depending on soil type. Blocks are formed with relatively simple and inexpensive hand-operated machines. Workers building the project could make the CEB themselves. Another advantage is that block dimensions are uniform, reducing the amount of mortar needed in a wall. It is also possible for the manufacturer to make custom-sized molds for blocks. CEB production requires some basic training, which leads to its disadvantages.
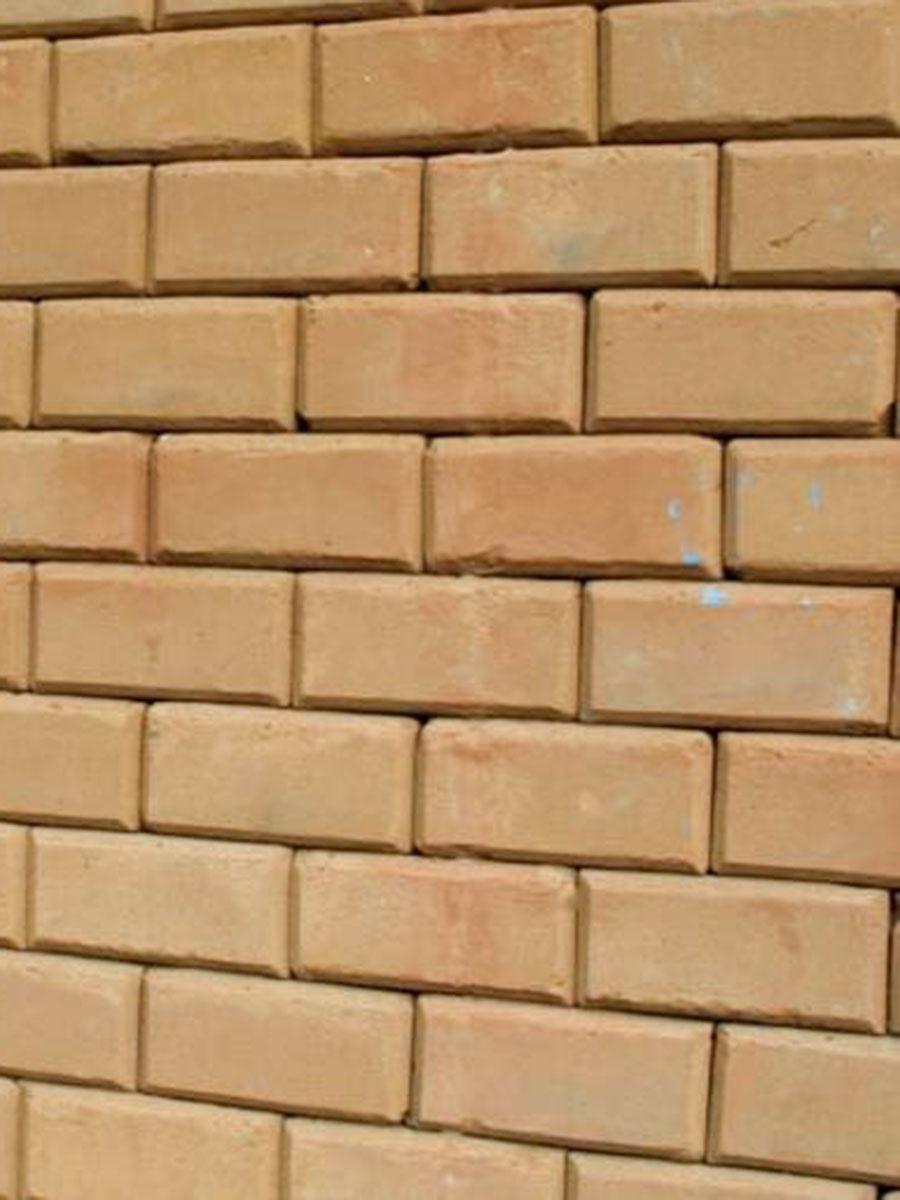
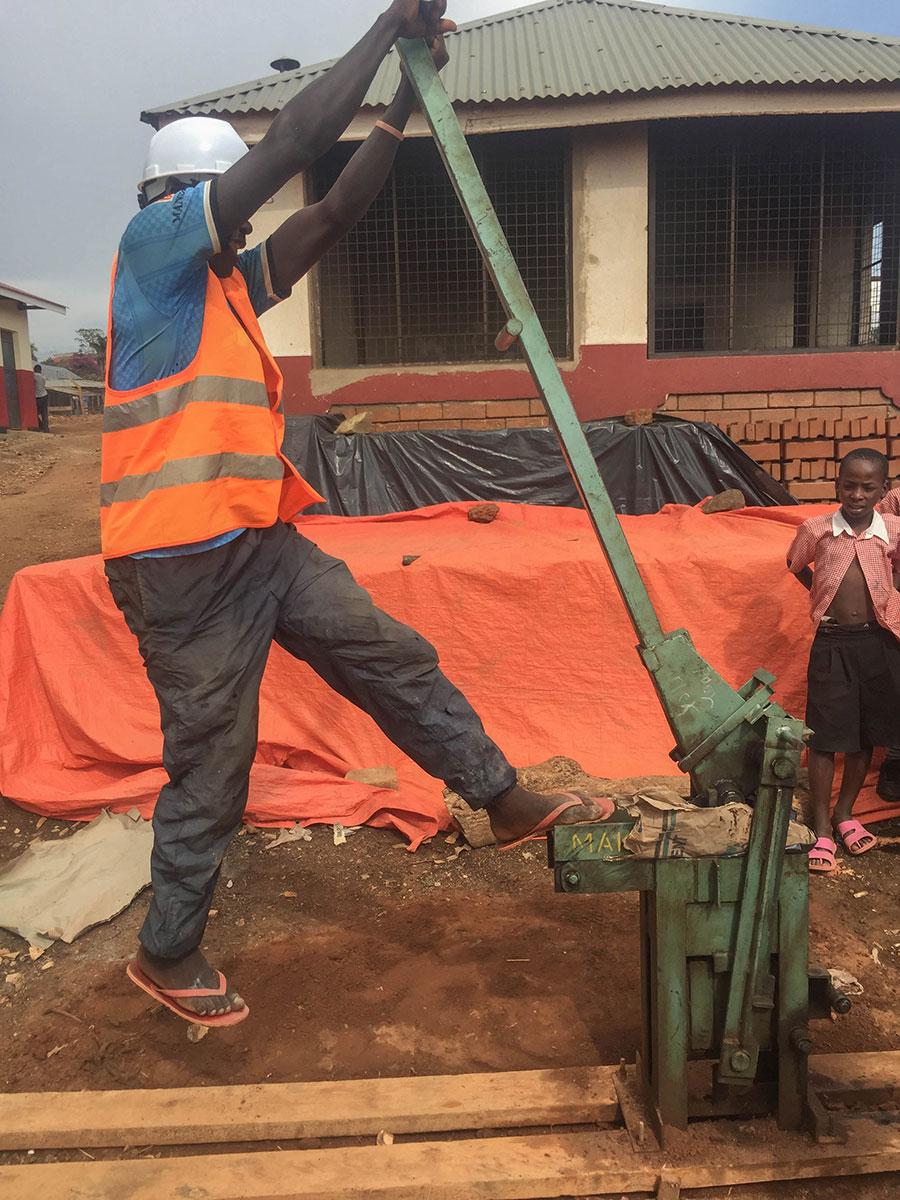
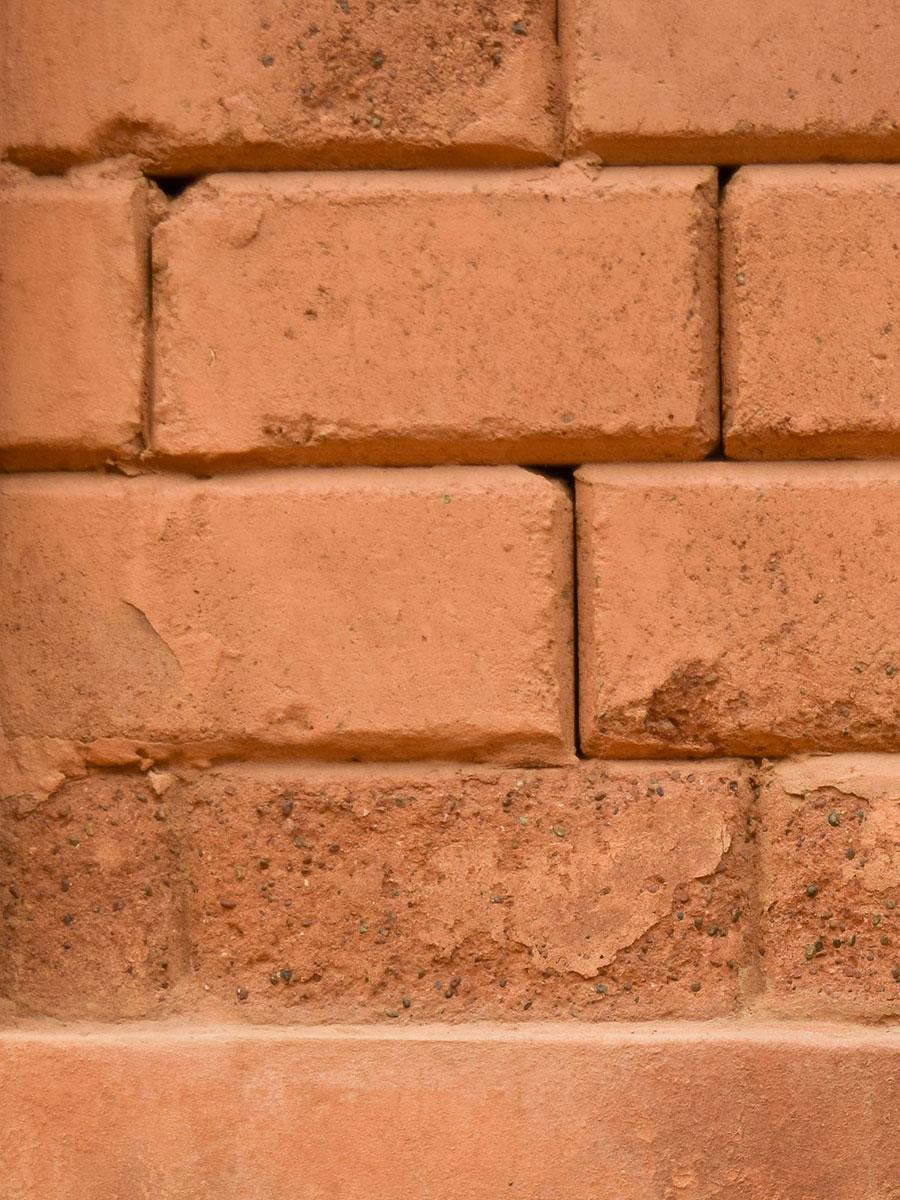
With inconsistencies in the soil and the process followed by people making the blocks, CEB quality can vary dramatically. Because cement is used as the stabilizing agent, good curing is required to achieve strength and durability. When CEB are produced in hot temperatures, exposed to direct sun and wind or where there is limited or difficult access to water, it is a significant challenge to keep the blocks adequately moist during the hydration/curing process. Another disadvantage is that CEB is susceptible to weather. If not made properly, they can degrade quickly when exposed to rain. CEB can be a good wall material; however, it is generally not as easy as the marketing materials make it sound. The ability to measure soil types, a good understanding of their dynamics, and strict control of the mix ratios are necessary. In certain situations, where the soil is the right consistency and there is proper oversight, CEB can be an appropriate solution. Besides use in buildings, CEB could be considered for low-cost walls to enclose a compound.Note 2
Local Brick
By far the most common wall material in Uganda and across the majority world is locally-produced brick, also referred to as ‘village brick.’ This type of brick is almost universal and has been produced in a similar way for centuries. People simply dig clay out of the ground, form it into bricks with wooden molds, and let it dry in the sun. Then they stack it to form large ‘clamps’ that function as kilns to fire-cure the bricks with wood over a period of days or weeks. The quality of clay, and therefore quality of brick, may vary significantly from place to place. This type of brick is inexpensive because of the low production cost and local manufacturing method. Local brick is widely available and is what builders and masons are most familiar using. In Uganda, these bricks are laid rather roughly in thick mortar joints due to inconsistency in brick dimensions. Afterward, the local brick wall is typically plastered to create the finished wall surface. As a result, though the bricks themselves are inexpensive, the finished wall can be fairly expensive because of the amount of mortar used and plaster work.
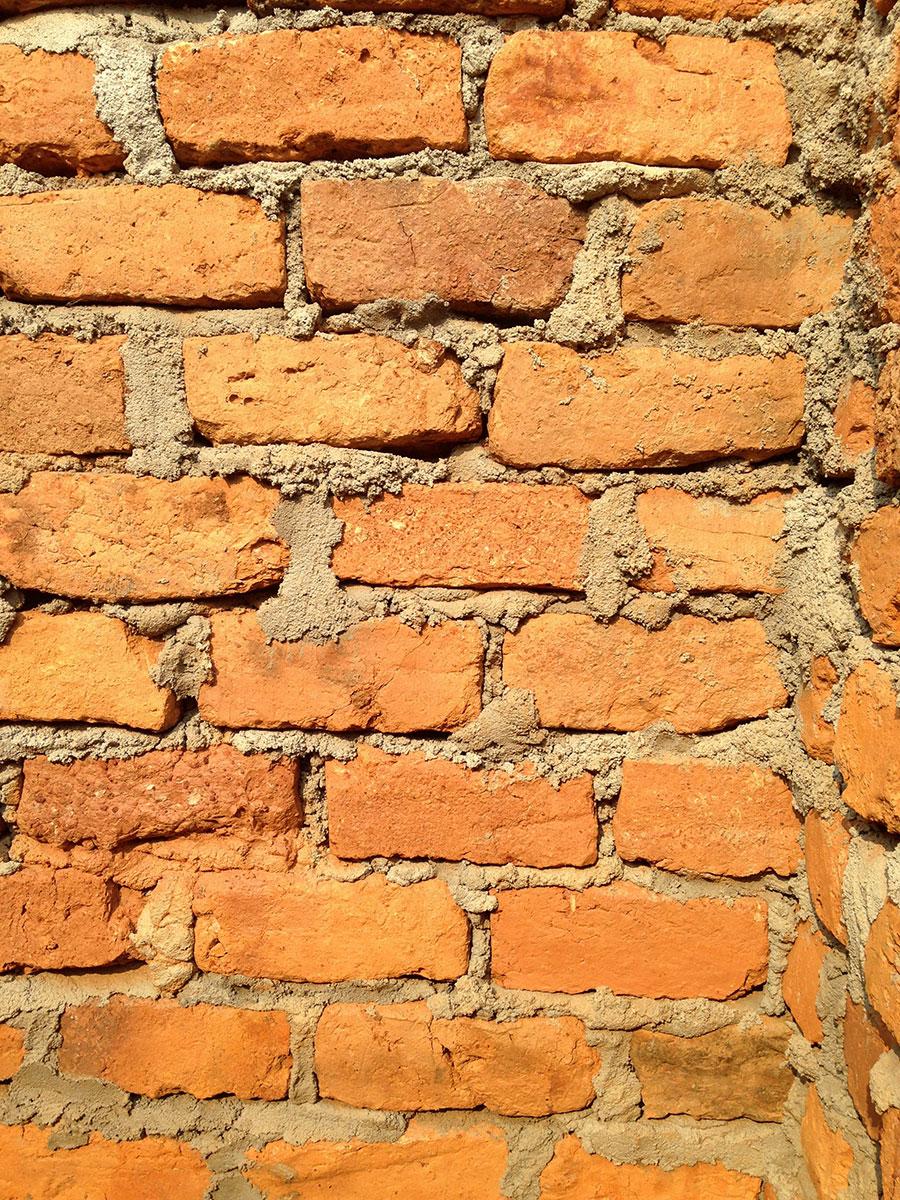

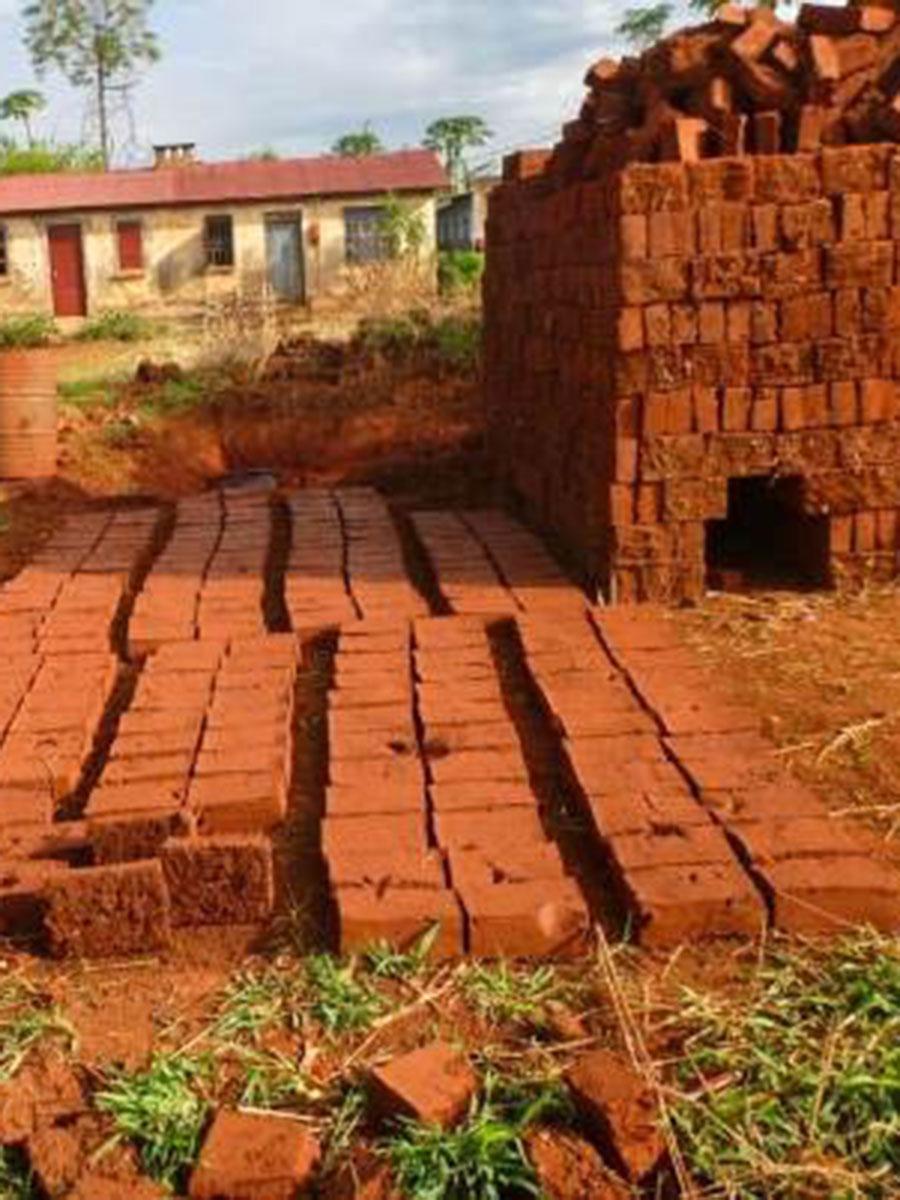
The nature of the firing process and the location of individual bricks within the ‘clamp’ results in inconsistent brick quality. Water absorption can be high and breakage during transportation to the construction site can be significant. Without sufficient data on material properties, EMI has traditionally not considered local brick a structural material.Note 3
EMI Uganda has found ways to omit plastering walls made of local brick. This not only reduces plastering costs, but also minimizes future maintenance costs associated with the common problems of spalling plaster and blistering paint. Over several years, EMI Uganda architects worked with construction managers to train masons to carefully select unbroken bricks and lay them neatly with much less mortar. Rather than plaster, a polyurethane coating is applied to the wall to protect the porous local brick from the weather. To most westerners, this is an attractive appearance. However, to most Ugandans, these buildings look unfinished—though there are indications this view is changing.

One last consideration is that the firing process for this type of brick uses great amounts of wood in an unsustainable way that contributes to deforestation. Researchers in the UK concluded that this type of brick produced in Uganda is 60% more energy-intensive than generic brick.Note 4
Factory Brick
EMI Uganda has also designed and built projects using factory-produced brick. Although these are not available at all locations, they are found in most cities. This type of brick is commonly used in the West. Factory production means the brick has a consistent quality, both in terms of appearance and strength. Brick strength is reliable enough that they can, under certain circumstances, be used as a structural material in two-story buildings.
Although factory brick is more expensive than local brick, it is durable and has a finished appearance. This means they don’t need heavy mortar between joints, or plastering, or a sealer coating. Laying them is also faster because of their uniform size and shape. In some cases, the final cost of a factory brick wall can be about the same as (or even less than) the cost of a finished local brick wall. However, this means training masons to lay the brick more precisely with much less mortar.
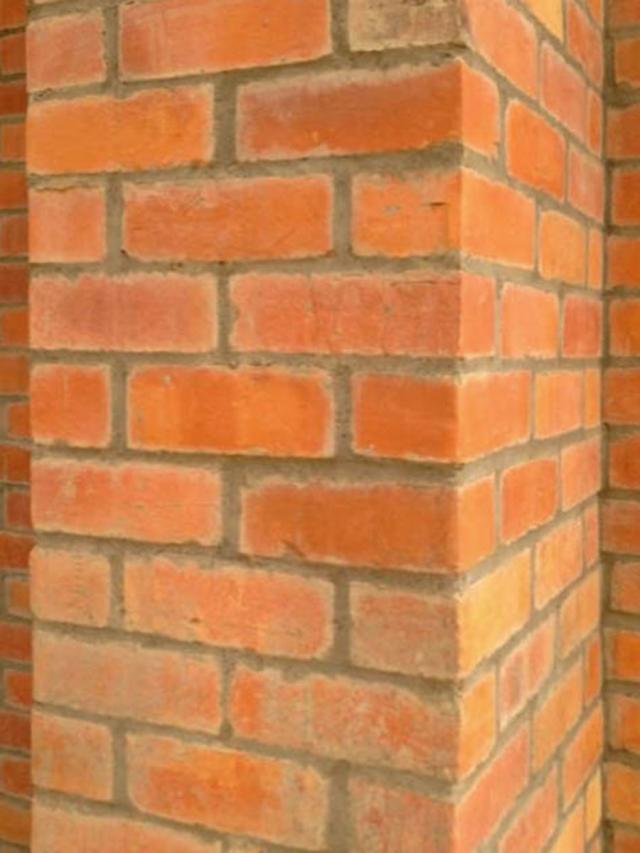
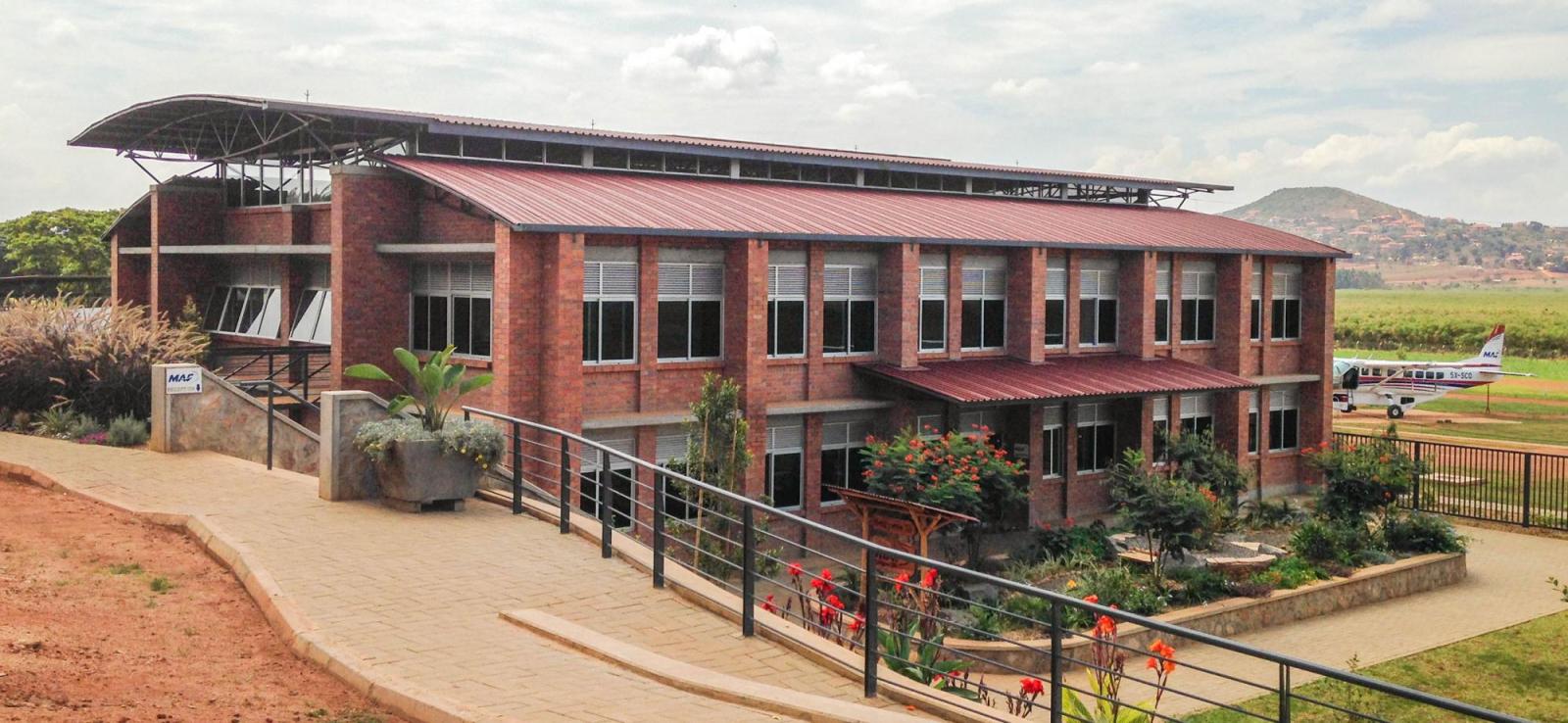
EMI Uganda’s most significant project using factory brick is its own relatively new office building shared with Mission Aviation Fellowship at the Kajjansi airfield. These bricks have also been used successfully on primary and secondary schools by other organizations in Uganda.Note 5
Factory brick is fired in a much more sustainable way. The firing process only takes a few hours and often uses agricultural by-products from coffee, sugarcane, bananas, and coconuts as part of the kiln fuel.
Concrete Block (Concrete Masonry Units)
A final wall material available in East Africa and much of the majority world is concrete block, or concrete masonry units (CMU). Although some are produced locally in small-scale factories akin to local brick production, here we are describing factory-produced CMU. Like factory-produced brick, CMU are available in cities and have a consistent quality. They are the most expensive wall material because of their cement content, but they also have the greatest structural capacity.
Yet when costs are considered as a whole, and due to their higher strength and much larger coverage area, CMU walls may not be so different in cost compared to walls made of local brick. This is because CMU walls can be thinner with less mortar and plaster used, and it takes significantly less time to build a square meter of wall area. CMU tend to be used on projects with higher budgets like private homes, commercial apartments, shopping centers, or upscale hotels. Since they don’t have to be fired—only cured, CMU do not require wood or other fuels in production. They are usually plastered to create the finished surface.
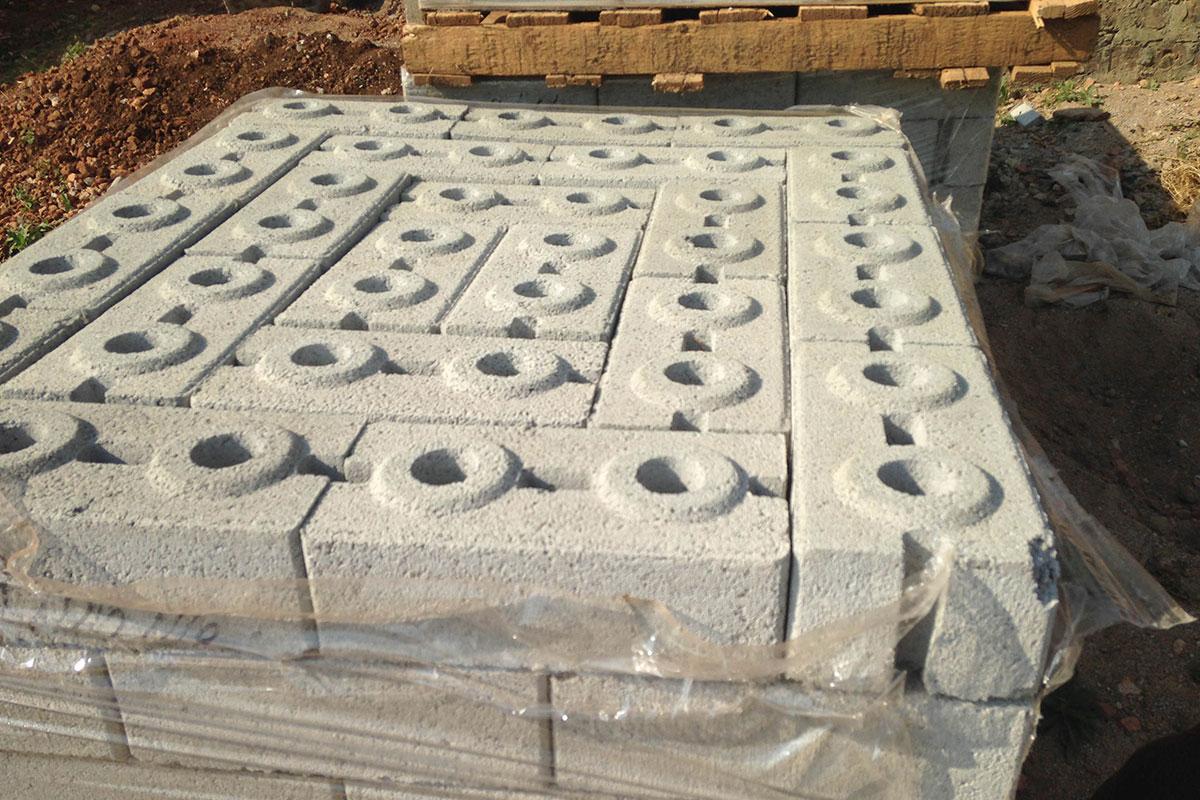
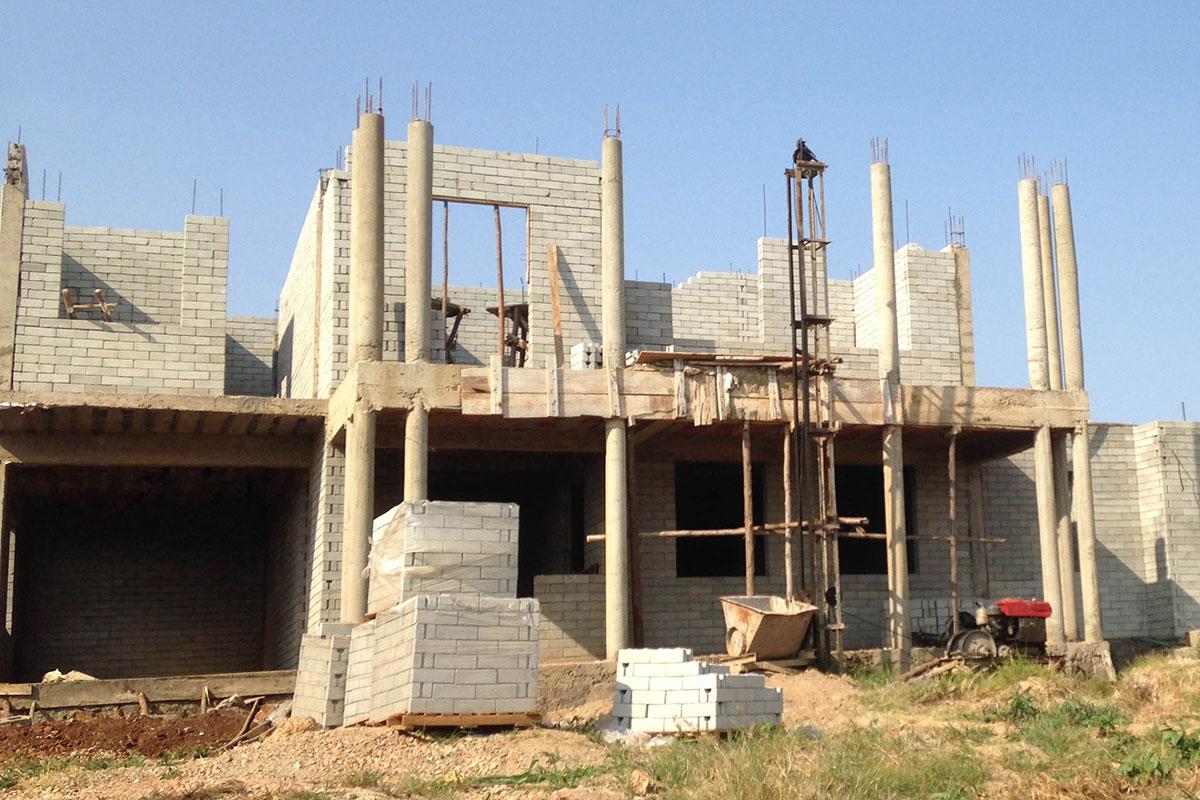
A note about thermal performance
Building walls are rarely insulated in many warm climates around the world. As such, the thermal mass of each wall material described above can reduce indoor temperature swings. Hot temperatures during the day are reduced and some passive heating is provided in the evening. However, in warm climates where night temperatures are not sufficiently cool, the heat radiating from the sun-baked walls in the evening can lead to uncomfortable indoor conditions. Better understanding of the thermal properties of typical wall materials, and subsequent appropriate design for the tropics is a topic of interest that the R&D department plans to investigate further in the future.
EMI’s architects, engineers, and construction managers strive to design and build projects that are sustainable, affordable, and culturally appropriate. This article is meant to introduce the choices and considerations for selecting the most appropriate wall material in East Africa for a given project situation.
The EMI Fund
The EMI Fund supports all that we do at EMI. With a strong foundation, we can keep designing a world of hope.
EMI Tech is looking for contributors – write to editor@emiworld.org with your topic and article outline.